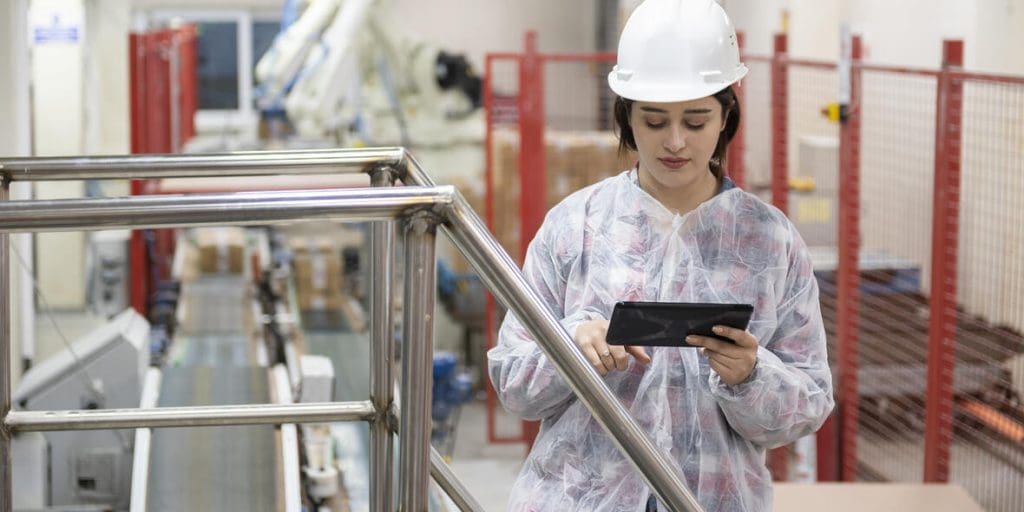
The Consumer Packaged Goods (CPG) industry is the foundation of modern society, providing access to essential goods, jobs, and community support. However, the industry is under significant pressure from the latest global megatrends, including responsiveness to supply chain disruptions, less predictable and higher energy costs, and difficulties attracting and retaining digital talent.
To address these challenges, CPG manufacturers need access to more insight-rich process and resource data across their entire value chain while still meeting operational and financial goals. Digital ecosystems and data sharing provide the foundations for a digital and sustainable transformation approach.
Converging information technology (IT) and operational technology (OT) at the site and company levels provides the essential data intel that can improve decision-making across the organization—from day-to-day matters like production, operations, and maintenance to strategic considerations to restore production, launch new products, or assess investment options.
Software-centric control: Digitalizing the complete operational lifecycle
The convergence of IT and OT, enabled by the internet of things (IoT), is changing the face of automation. Digitization, in particular, is charging the way forward for the CPG industry, enabling increased speed in process changes or decoupling software from hardware via simplified plug-and-play engineering. Meanwhile, software-defined automation at the edge prioritizes important data, minimizing latency and speeding up access to crucial information for optimized control.
Forget everything you know about automation. Today, it is software, not hardware, that is at the core of the industry’s future.
In an ideal modern manufacturing facility, all installed equipment–including ingredient tanks, silos, pumps, mixers, conveyors, robots, warehouse racks, or electrical panels– would be connected via sensors and monitoring devices to an open software-based control platform like EcoStruxure Automation Expert.™ This allows for a comprehensive, big-picture view of all equipment, assets, machines, and production lines.
This added insight simplifies and accelerates production lines’ design, operation, and maintenance. It reduces hardware constraints and minimizes interruptions caused by proprietary applications. The software-based control platform is interoperable with native and third-party devices, fostering innovation and reducing the total cost of ownership.
The next evolution of universal automation will be driven by dynamic resource modeling and open standards. EcoStruxure Automation Expert is based on this principle. The platform runs real-time operations control solutions, unifying people, processes, and assets across all facilities. This provides valuable context for operators, enhancing engineering flexibility and operational efficiency.
For example, Master Systems, an automation design company in South France, worked with Schneider Electric to implement the EcoStruxure Automation Expert solution for Sophim, a natural cosmetics company. The original facility design limited system evolutions, hindering the company from responding to new operational and production challenges.The new system, focused on flexibility, is scalable to enable potential event simulations or system changes, real-time maintenance, and easier upgrades, helping ensure that the company can meet future needs.
Operations data management trusted by engineers and IT alike
In CPG environments, the software control platform provides real-time contextualized data to cloud-based systems and applications, enabling end-to-end visibility. With AI-based analytics, it offers predictive capabilities, validates business decisions, sustainability tracking, and more, giving you the confidence of accurate and timely insights.
Alongside EcoStruxure Automation Expert, the Industries of the Future software-based edge automation and control platform, Schneider Electric offers an extensive application portfolio, facilitating business intelligence, analytics, and AI tools for industrial operators and management. Data generated from connected assets and processes can create dynamic visualizations and asset frameworks for contextual data insights.
Let me highlight one of these applications: AVEVA™ PI System,™ which collects, cleanses, stores, and enriches real-time data with sub-second granularity. With full IT compliance, the cereal giant Kellogg’s deployed the solution at its manufacturing plant in Spain, unlocking reliable data to remote users and applications for data-based decisions.
The plantwide digital transformation, including data analytics, provided major results: critical-control-point (CCP) incidents fell by 64%, and the number of cereal cases scrapped due to failures was reduced by 73%.
Accelerating digital to stay competitive in the market
Much of the automation in today’s CPG operations was designed decades ago, relying on hardware from a single supplier and predating modern computing power. With software-defined automation and open standards, existing complexity can be simplified, allowing manufacturers to easily change or update their systems whenever and wherever needed. This contextualized real-time data unlocks a world of digital applications and services that pave the way to sustainable performance, greater resilience, and talent retention.
What could this look like for you?
Imagine having contextualized real-time information that is easily accessible and displayed via a cyber-secured cloud data platform. Operators, production staff, maintenance teams, and managers receive alerts, identify issues, confirm status, and investigate events by analyzing all the digital information gathered from the connected assets (i.e., inventory levels, pump status, truck availability, etc.). They are each empowered to take immediate action to avoid disruption and downtime, improve operations, and maximize profitability.
To learn more, please read the Harvard Business Review Analytic Services white paper, “The Digital Path to a More Efficient and Sustainable Food and Beverage Industry,” which outlines the critical elements driving these changes.
Add a comment