This audio was created using Microsoft Azure Speech Services
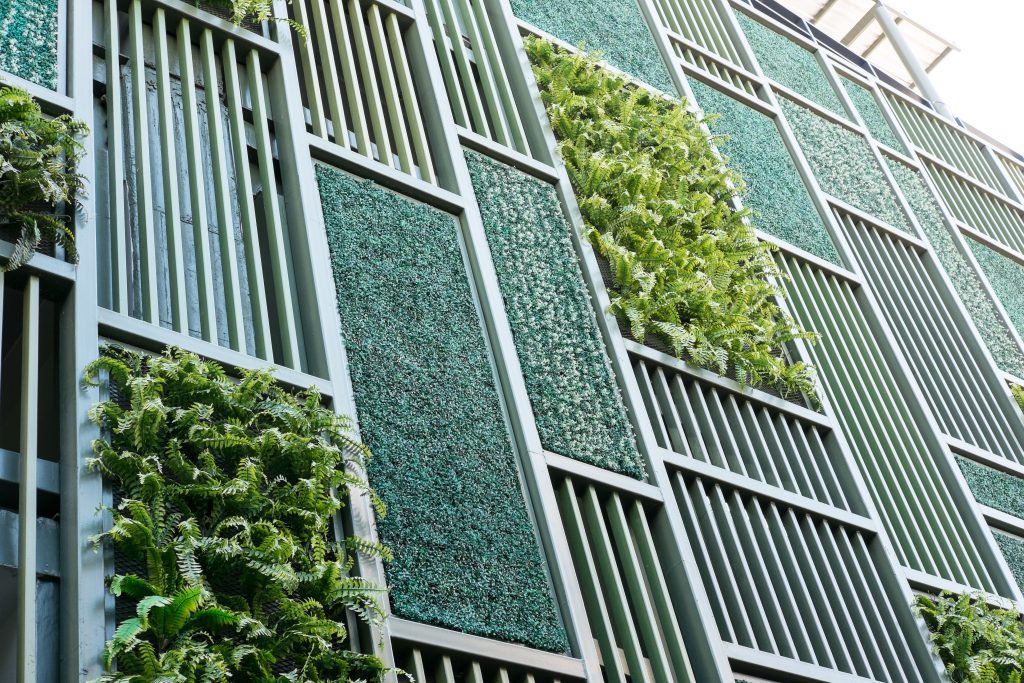
The “Green Steel” initiative supports clients in their move from fossil fuel-based to electrical energy-based steel production. While electrification is an effective way to decarbonize, this change leads to a few power quality-related challenges for clients’ existing grid associated with the addition of electric arc furnaces (EAF) and their specific load management
EAFs typically create quite significant disturbances in the supply system due to arcing. As a result, the bus used to supply such loads is referred to as a “dirty bus” and is kept separate from the “clean bus” system to prevent interference with this other unit equipment.
Before we have a look into the power quality challenges and the mitigation techniques let us look at the types of EAFs and their working principles. Broadly speaking one could have a conventional AC or DC furnace, or advanced versions of these. Examples are Q-one AC furnace (from Danieli) which is a thyristor-based multicell technology. Then there is the AURA DC furnace (from SMS) which is chopper-based multicell technology. One could also have a submerged arc furnace design.
How does an electric arc furnace work?
An EAF is a type of furnace that utilizes electricity to create a high-intensity electric arc. This arc is formed between electrodes, commonly composed of carbon or graphite. On application of high voltage, the air between the electrodes becomes ionized, establishing a conductive path. As a result, the electric arc generates extreme heat. This intense heat serves to melt and refine scrap metal, predominantly steel, that is placed or dropped within the furnace often through a mechanical system like a crane or a conveyor belt with monitoring and control capability. The resulting molten metal (in various grades) can then be extracted and utilized for a diverse range of industrial applications.
Power quality issues related to electric arc furnaces:
- Low power factor:
A higher power factor indicates more efficient utilization of electrical power. The optimum power factor is unity (1.0), and any value below that indicates a need for extra power to accomplish the intended task. Hence, poor power factor causes higher current losses and voltage drop in the system and more load on the environment (COX, NOX, SOX).
In many countries, technical regulations specify that the power factor at the point of common coupling should ideally be > 0.95 PF.
The operating power factor of furnaces typically ranges from 0.15 PF (below this there will be no arc) to 0.85 PF (above this the arc will be unstable), with an average value of around 0.76 to 0.8 PF. However, when employing advanced multicell technologies, the average value can be enhanced to approximately 0.93 to 0.95 PF based on combined statistical values evening out the issue.
- Harmonics:
In an electrical power system, a harmonic of a voltage or current waveform is a sinusoidal-shaped wave with a frequency that is an integral multiple of the fundamental frequency. These harmonic frequencies are generated by non-linear loads such as furnaces, rectifiers, and various other equipment. Such harmonics as a result can lead to overheating, vibrations, audible noise, etc., thereby reducing the equipment and power infrastructure lifespan and efficiency.
The most dominating harmonics produced by EAFs are the 2nd, 3rd, 5th, and 7th harmonics. It is not possible to calculate it precisely; it can only be estimated using available references or based on past experiences.
The magnitude of harmonics is influenced by factors such as metallurgical practices, the composition of the charge mix (with scrap contributing to significant disturbances), power factor during operation, electrical balance (which encompasses electrode length), and potential resonance within the mechanical system. The electrical and process controls therefore are to be designed to minimize impact and maximize resilience.
- Flicker:
Power-line flicker occurs when the voltage of the power supply fluctuates rapidly due to changing load currents, resulting in visible changes in the brightness of a lamp over time causing eye strain and a detrimental impact.
Flicker is characterized by voltage variations within the range of ±10%, causing perceptible changes in light output. Higher frequency fluctuations can lead to more pronounced flicker, especially in lighting systems, causing visually disturbing rapid changes in brightness.
The flicker in the AC EAF is around 1.5 times higher than DC EAF at the same range of
maximum power.
Power compensation system to improve power quality:
Reactive power is an essential component in an electric power system and significantly influences the power quality. Reactive power compensation is the process of adding or injecting positive and/or negative VAr’s to a power system.
Classification of PCU:
- Static compensation:
Static compensation comprises fixed capacitor banks (used to improve power factor) and series reactors (used to tune for a particular harmonic). It provides a minimum impedance path to a particular harmonic current and traps the same. Therefore, it can be utilized to improve power factor and mitigate harmonic content.
- Dynamic compensation:
Dynamic compensation is mainly used to suppress flicker generated by the furnaces. It may be of static var compensator (SVC) type or static VAR generator (SVG)/STATCOM type. Typically, the SVC has a response speed of 20-40ms, while the SVG’s response speed is less than 5ms. The rapid response of the SVG significantly enhances its ability to suppress voltage fluctuation and flicker.
Hence, their selection depends upon the flicker severity factor or required flicker reduction factor.
Power quality plays a critical role in Green Steel
As we know, from a process point of view the equipment related to EAF is highly specialized, and the system relies heavily on it. Any failure in this system can lead to significant production losses and can also negatively impact other related departments such as DRI, RH/VD, and Caster
From a power point of view, it is important to keep electrical pollution level within the specified limit otherwise it can have various detrimental effects on system performance, including reduced efficiency, increased failure rates, and higher maintenance requirements.
Additionally, meeting electrical regulations is crucial as there are strict norms in place. Failure to comply with power quality standards at the point of common coupling may result in substantial fines.
Choosing the right equipment for your power compensation unit is vital for ensuring the reliability and maximum availability of your system. Therefore, the users must obtain the right advice.
Want to learn more? Download my latest paper: Power distribution system and related challenges in Electric Arc Furnaces
Contact me if you have any questions or suggestions.
Add a comment