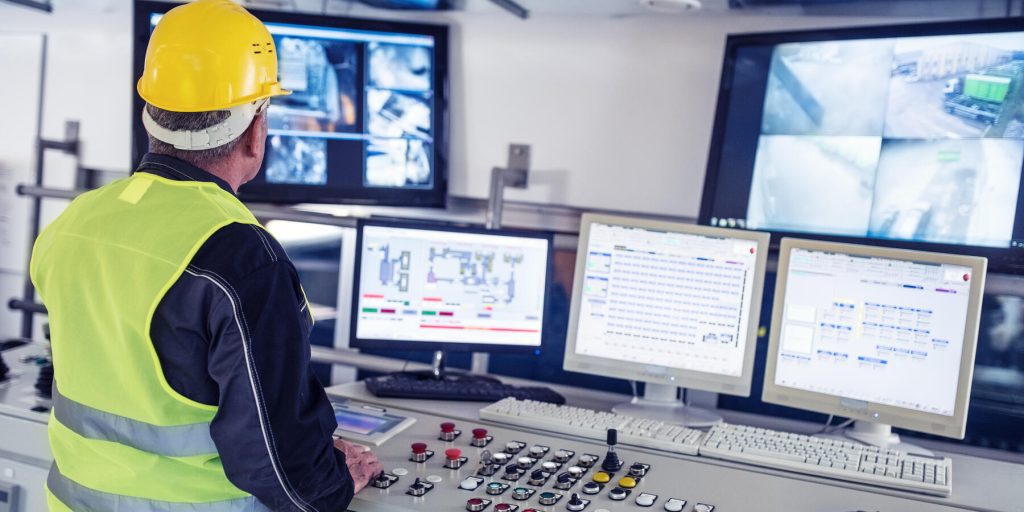
Designing and building industrial automation systems often focuses on hardware and connected devices. However, in the wake of complex digital transformations, there is an appetite for achieving safety and security with whatever automation configuration is designed and developed. Software-defined automation is a new paradigm shift, offering original equipment manufacturers (OEMs) portability and interoperability while affording flexibility and scalability.
For decades, the transition from mechanical systems to electronic controls, such as PLCs and SCADA systems, has propelled OEMs towards higher efficiency and machine reliability. Yet, as industrial automation advances, its current iteration often fails to meet today’s demands for rapid product development and flexible production lines. In this fast-paced environment, traditional systems hinder OEMs’ ability to adapt swiftly, leading to excessive engineering efforts and costs.
A new way to approach industrial automation
Software-defined automation is a new approach that uses software tools and methodologies to drive the process.
In a joint white paper between Frost & Sullivan and Schneider Electric, entitled “Software-defined Automation for Future-ready Machines,” the authors explain “using computing power in virtual machines as a substitute for control and automation via hardware assets.”
In this new era of optimized equipment performance and sustainability, digital transformations are driving companies to embrace a software-defined automation model to help:
- Shorten lead times while enhancing maintenance processes
- Reduce operating costs
- Improve operational flexibility through modularization
- Simplify utilization of artificial intelligence (AI) and machine learning (ML) methods
- Optimize resource use and support circular economy initiatives via more sustainable manufacturing practices
Smoother integration of IT and OT
Information technology (IT) and operational technology (OT) systems integrate smoothly when logic and intelligence are centered on software instead of hardware. Technology is now more versatile and can connect more easily with other devices and systems. System-agnostic solutions may be more easily suited to manufacturing configurations and customized to processes without the burden and cost of a customized solution. To realize these benefits requires understanding the utility of software-defined automation and having confidence in its efficacy.
Manufacturers are steadily embracing software-defined automation (underpinned by IEC 61499) to help improve portability and interoperability and bridge IT and OT. This shift is timely as applications like virtual PLCs and digital twins are set to play a disruptive role in smart factories. Software-defined automation optimizes manufacturing processes and fosters predictive maintenance and quality improvement. It also seamlessly integrates with new and existing automation systems and designs.
Software-defined automation, however, is a new model to many and requires expertise to implement and integrate. As the industry pivots towards this model, OEMs must consider strategic partnerships with technology experts who offer the necessary expertise and proactive support. To ensure a cost-effective transition, start with a pilot project, enhancing legacy systems with added functionality and flexibility without needing a full overhaul.
Agility in response to new and future customer demands
As further noted in the new white paper, “For machine OEMs, the simplicity of engineering that comes from adopting a software-defined approach improves agility in responding to end-user demands for customization, expansion, integration, or new functionality. This helps avoid the need to manufacture multiple versions of the same machine, reduces time to market, and supports revenue growth for OEMs.”
To learn more about the benefits of software-defined automation, download our white paper, “Software-defined Automation for Future-Ready Machines.”
Add a comment