This audio was created using Microsoft Azure Speech Services
Industrial companies manufacturing consumer packaged goods know that embracing sustainability and digital transformation is critical for continued growth in today’s uncertain market. Climate issues loom, and energy costs rise. Organizations must find ways to improve energy efficiency, embrace renewable energy sources, and fully electrify their operations.
The question is: how?
The reality is if you want to embrace sustainability, you need to digitalize. Digitalizing your systems and enhancing data gathering can help unlock the power and extra capacity within your physical asset base, but it needs to be connected – and secure. Cybersecurity is inextricably linked to digital transformation. Managing cybersecurity risks is the starting point for digitalization and often the foundation for further industrial sustainability.
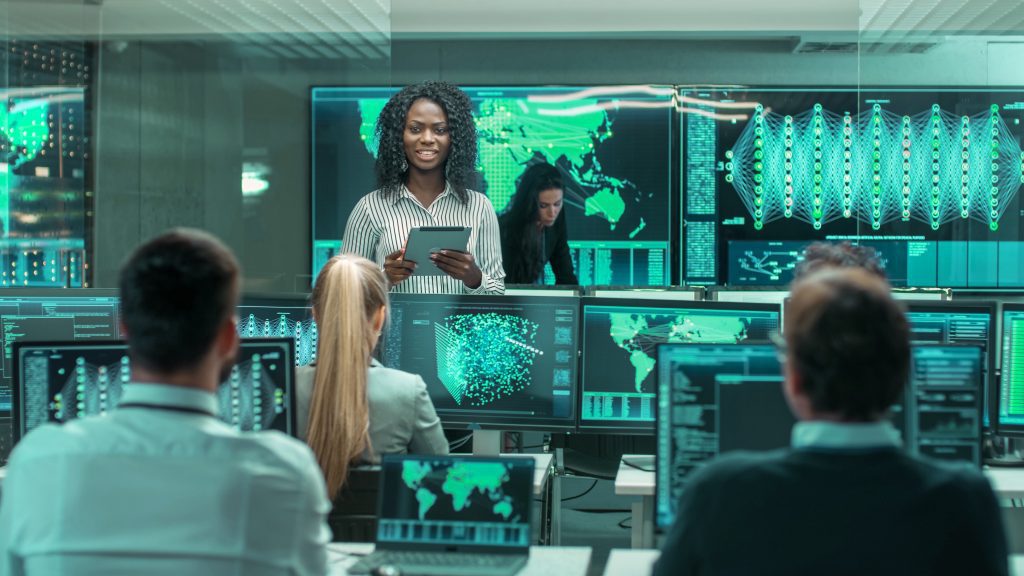
As part of a digital transformation effort, you need to define guidelines, gather data, update and standardize processes and procedures, ensure redundancy, harden platforms, and engage cyber assurance services. These steps are necessary to achieve top-line growth because they maximize operational efficiency, reduce waste, enhance workplace safety and compliance, empower workers, and optimize asset usage.
Ultimately, all these elements contribute to business continuity. Missing or ineffective management of a digital transformation project opens a company to financial exposure. It boils down to lost revenues. In fact, a 2022 McKinsey report shows that large-scale corporate transformation projects fail about 70% of the time. And this statistic illustrates the reality that digital transformation is not easy. It’s a complex process that needs discipline and a proven methodology to be successful. But it also needs a real-world understanding of how things work in an industrial setting.
The right consultant makes all the difference
Buyer beware: not all digital consultants are the same. Most lack real-world manufacturing experience and are armed only with theories or generic software knowledge. Some come with just consulting expertise. This is one of the critical ways that companies like Schneider Electric separate themselves from the others. We are a manufacturing company with the same challenges you see within your organization. Like you, we own factories, manage supply chains, and understand industrial companies’ practical challenges, whether they are oil and gas producers or pharmaceutical manufacturers. And what we’ve learned in our own facilities can help other companies gain the same success.
Manufacturing is a complex and multifaceted challenge that cannot tolerate extended downtime. So, when you are choosing a digital transformation consultancy team, be sure to look for one that offers a specialized, end-to-end service designed to accelerate successful digital transformation strategic planning and implementation for industrial businesses, focusing on sustainability, industrial performance, digital operations (including cybersecurity), energy management, and return on investment.
Optimizing operations over the long run
Digitalization is the core of modernizing industrial facilities – the Fourth Industrial Revolution (4IR), as it is commonly called. The goal is to bring plants still running older systems up to the current standards and optimize them for future growth. However, this must be an ongoing modernization process, as industrial equipment can have a very long lifespan. It is inefficient (both financially and in terms of embodied carbon) to replace technology that still works.
Consultants must help companies maximize the value of yesterday’s technology for today while strategically addressing technical debt and laying the groundwork to thrive in the future. We focus on making the most of what already exists. We consider the practical realities of our customers’ environments and demonstrate actual commercial outcomes that justify project costs and positively impact the bottom line. A successful transformation must be tailored to the company’s specific targets. It is broken down into smaller steps that achieve tangible business outcomes while preserving as many existing assets as possible and connecting them in practical and affordable ways to serve the larger project goals.
Trust must be earned through experience
When choosing a transformation partner, doing homework and checking references is critical. For example, Schneider Electric started redeveloping how it manages its factories in 2017. We have been ranked number one in the Gartner Supply Chain Top Companies for 2023 because our digital transformation has revolutionized how we do business.
We also regularly rank as one of the world’s most sustainable companies, ranking number one in Sustainability Magazine’s list of Top 100 Companies. Again, this area of expertise has been a focus for our company and our customers. It gives us a deeper perspective into what our customers want and need.
In fact, Schneider Electric is one of the few companies worldwide that has earned multiple awards from the World Economic Forum for its global smart factories and distribution centers, dubbed Lighthouse Factories. These factories have taken 4IR technology from pilot to integration at scale to transform operations, value chains, and business models for compelling financial, operational, and sustainability returns. These factories act as beacons for other factories looking to apply advanced technologies to their operations.
Look for a customer-oriented approach
When considering or continuing a process of digital transformation for your company, take the time to choose the right partner for your project and organization. A trusted partner with experience. One that complements your business needs will speed your time to results and ultimately help ensure your long-term success. Evaluate which solutions and services are required within your organization:
- Overall framework design
- Demand analysis
- Smart factory blueprint and implementation planning
- Operation & real-time analytics
- Cyber-security and secure remote access
- Predictive maintenance
- Performance and energy monitoring
- Utilities performance optimization
- Alarm and network performance management
- Accelerated value delivery
- Paperless workflow management
- Traceability
- Safety management
Examine their methodology to ensure it will provide everything you need to achieve your transformation goals. Whether you are focused on quality, for example, with a goal to reduce parts-per-millions defect ratings, or productivity and capacity gains by improving overall equipment effectiveness or labor efficiency, several crucial elements should be included:
- A consultative approach and a clear understanding of your business needs and goals
- The capacity to deploy at scale
- Previous experience with lean consulting, particularly around cost optimization and efficiency improvements
- Strong customer references that demonstrate trust relationships
- Strong segment knowledge of industrial manufacturing processes and best practices
- Strong cybersecurity skills
- Portfolio to provide a single, cohesive solution without the use of multiple sub-vendors
Charting your customized transformation
When considering or continuing a digital transformation for your company, take the time to choose the right partner for your project and organization. Find out more about our Industrial Digital Transformation team and its approach to digital transformation consulting and deployment.
Add a comment