This audio was created using Microsoft Azure Speech Services
Industry is Brazil’s second-largest sector and represents almost a fifth of the overall GDP. But industrial operations in Brazil now face many challenges to increasing productivity and profitability while maintaining safety.
In this post, I’ll discuss three critical threats industrial organizations in Brazil are currently navigating and how they can be overcome with a new vision, new digital solutions, and the support of an expert partner. For perspective, this is a subject that I understand well since Westcon is a pioneer in industrial automation and has operated in the Brazilian market for more than 25 years.
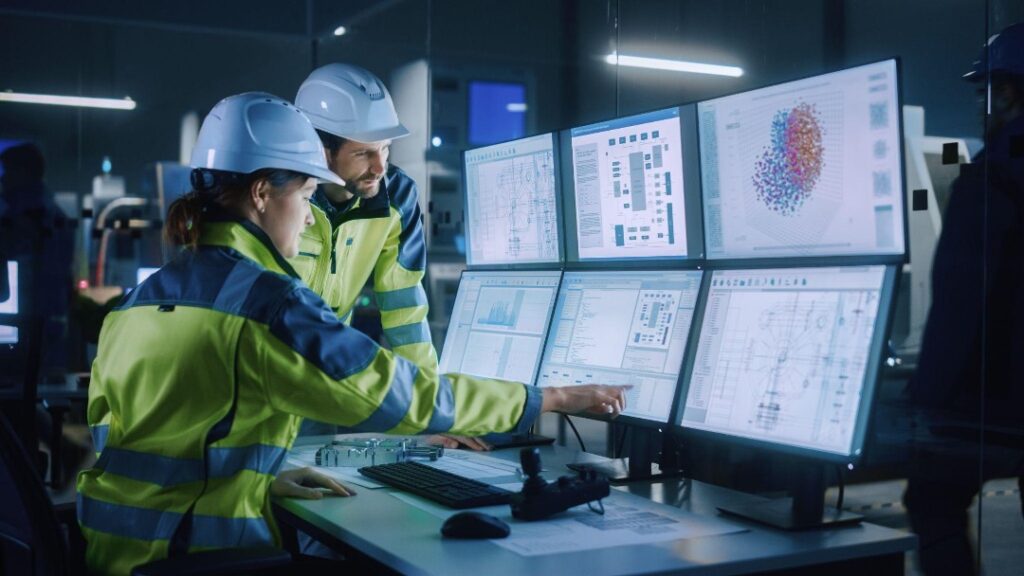
Risks to profitability and continuity in industrial operations
Three conditions are proving to be substantial threats to industry in Brazil:
- Natural gas and electricity prices are rapidly increasing. Brazil’s gas and electricity prices are among the world’s highest (when adjusted for per capita income). In the first half of 2022, average power tariffs increased by 11.6%. These rising energy prices significantly impact industrial operating expenses (OPEX) and, in turn, profits.
- In the first half of 2022, Brazil suffered 31.5 billion attempted cyber-attacks – a 94% increase over the same period last year, making it the second most targeted country in Latin America, behind Mexico. One in four companies experienced an attack in 2021, and industrial operations are not immune. In 2017, oil company Petrobras suffered a ransomware attack, while a Norsk Hydro aluminum plant in Brazil was similarly attacked in 2019. These cyberattacks can be costly and shut down entire operations – weakening confidence in a company’s ability to protect data and deliver on time.
- Brazil’s recent slow economic growth – which some analysts attribute to low productivity and lack of innovation as contributing factors.
Adopting new, cyber-secure digital technologies for industrial operations can help reduce these threats, improve productivity, reduce OPEX and downtime, and support decarbonization goals.
Embracing Industry 4.0 and beyond
Many industrial businesses in Brazil are now following the Industry 4.0 trend, with intelligent, autonomous machines being more connected and integrated. Digitalization using the industrial internet of things (IIoT) and the cloud enables much greater access to data across the factory floor.
Hyperautomation takes this further, converging IT and OT by integrating business process management and process automation.
Regulations are partially driving these transformations. But digitalization’s main driver is creating a connected enterprise that enables data-driven decision-making. Data access can help plant managers identify energy, process, and maintenance inefficiencies that are wasting money and impeding productivity and sustainability.
However, it’s not enough to connect systems and access more data. The key to success is tools that help you make sense of that big data and give you the insights you need to act.
Make the mindset shift from hardware to software solutions
Today, process automation is more than just hardware devices like sensors, VFDs, PLCs, and HMIs, which are progressively becoming commoditized. The transformation to next-generation automation depends on the software that supports smarter operations that are more sustainable and resilient.
Advancements in site- and cloud-based software and other digital technologies enable:
- Data to be securely aggregated from all systems across your plant
- Analytics that feed dashboards with KPIs to help you continuously monitor performance
- Wasted energy or other valuable resources to be revealed
- Problems in your production lines to be identified and isolated
- Determination of older automation hardware that is running inefficiently and needs replacement
Advances in artificial intelligence (AI) and machine learning help smart machines get smarter and identify performance degradation or other machine characteristics that were previously invisible. You can then take action before issues can cause damage or downtime.
Deep insights like these allow companies to make better, faster decisions that improve efficiency, maintenance, and uptime. All of these translate to savings in OPEX. Cloud-based reporting also makes collaboration and sharing best practices with other plants easier.
Partnering to put innovation into practice
If you want to transform your plants through digitalization and Industry 4.0, you need an experienced partner with the solutions and relationships to guide you there. A trusted partner can help your company move more quickly – saving you time, resources, and money.
Westcon has extensive experience across many sectors in Brazil, and we’ve been recognized as a pioneer in industrial automation and network technologies. For decades, we’ve been working with customers to help them modernize their operations in automotive, oil and gas, and pulp and paper, as well as with large-scale infrastructure operations like water and wastewater, energy, ports, harbors, airports, and more.
Westcon differentiates by offering and supporting complete solutions. We have close partnerships with experienced systems integrators and leading technology and service providers like Schneider Electric.
We’ve been an Alliance Certified Industrial Automation Distributor partner for Schneider Electric since 2019. We were recently recognized as a global partner of the year for our excellence and achievements in 2022.
To help our customers on their industrial digital transformation journeys, our in-house team offers a unique level of knowledge in automation, safety, IT/OT cybersecurity, and other disciplines. We also train our customers and integrator partners to maximize the benefits of digitalization. These capabilities separate us from business consulting companies.
Recently, we were involved with a large LNG terminal project in northern Brazil. This complex project included floating storage and regasification, a three-kilometer pipeline, and a receiving station initially serving industrial and power companies. By leveraging our unique expertise and knowledge of local regulations, we collaborated with the customer to understand their challenges and propose the best solution. We then provided system design support and worked closely with the systems integrator to deliver a complete automation solution for the LNG receiving station, pressure regulation system, odorization system, and metering system.
The heart of our solution is AVEVA™ Plant SCADA software. This integration delivers powerful visualization with a holistic view of all operations to help ensure safety, reliability, productivity, and sustainability. It is a scalable, flexible, and easy-to-use solution that has accelerated the digital transformation of this site and will enable cost-effective future expansion and fast replication at other projects.
Like many of the manufacturing solutions we provide to our clients, it offers connectivity at the automation level and a simultaneous, cyber-secure data connection to cloud-based apps like EcoStruxure Machine Advisor. Cloud platforms offer powerful analytics, simple scalability, and remote monitoring with secure data access for facility teams. Backed by the world-class expertise of Schneider Electric, Westcon is at the forefront of technology, including the industry shifts to open, software-centric automation for Industry 4.0 and beyond. For more information, read Schneider Electric’s E-Guide on “Seizing the digital opportunity” to understand more about the value that partners add along this journey.

Westcon Redes e Conectividade Industrial
Westcon is a recognized leader in the industrial automation market, providing professional services such as analysis, diagnosis, troubleshooting, and network certification. As a pioneer in the execution of these services, Westcon is known for having a team of experts in various areas of industrial automation. They have been involved in a range of successful projects over their 29 years of operation.
Schneider Electric Alliance Partner Program
Through the Schneider Electric Alliance Partner Program, we empower companies to develop new capabilities to better support the digital transformation of customers and work in partnership to strengthen business resiliency.
Conversation
Very good
nice article. i loved it