Depuis bientôt 100 ans, Minitubes fabrique à Grenoble des produits tubulaires métalliques de très haute précision, exportés dans le monde entier. L’entreprise vient de se doter de technologies digitales de pointe, qu’elle a commencé par tester sur un nouveau banc d’étirage. Pour quelles raisons et avec quels résultats ?
C’est l’histoire d’une entreprise familiale détentrice, depuis 4 générations, d’un savoir-faire très spécifique ; celui de fabriquer des tubes ultra fins, de haute précision, d’une qualité irréprochable. Car ces tubes sont utilisés en médecine (implants cardiovasculaires, cathéters, aiguilles… pour 90% de l’activité) et dans certaines industries de pointe (automobile, aéronautique…). Et utilisés de plus en plus puisque l’entreprise Minitubes est passée de PME à ETI en moins de 2 ans, portée par le développement de ses clients historiques et des nouvelles techniques de soins, moins invasives.
Pour accompagner sa croissance, Minitubes engage de nombreuses transformations dont l’extension de son outil industriel avec le déploiement de standards d’organisation et de digitalisation.
Parce que ses métiers sont très spécifiques, l’entreprise fabrique elle-même ses équipements de production. C’est ainsi qu’elle a lancé courant 2023 un projet de développement d’un nouveau banc d’étirage, conçu par son bureau d’étude interne. C’est Schneider Electric qui est choisi et les deux entreprises collaborent pour trouver les meilleures solutions digitales pour l’automatiser, le programmer et le piloter.
Pour ce type de produit, les spécifications sont difficiles et les tolérances très réduites. Le produit subit de fortes contraintes mécaniques puisqu’il faut étirer des tubes métalliques de quelques centimètres de diamètre à quelques dixièmes de millimètres, en respectant les caractéristiques tout au long des pièces. De plus, la production doit rester identique, au même niveau de qualité, tout le temps, avec une cadence de fabrication élevée. Car pas question qu’une pièce ne sorte des spécifications !
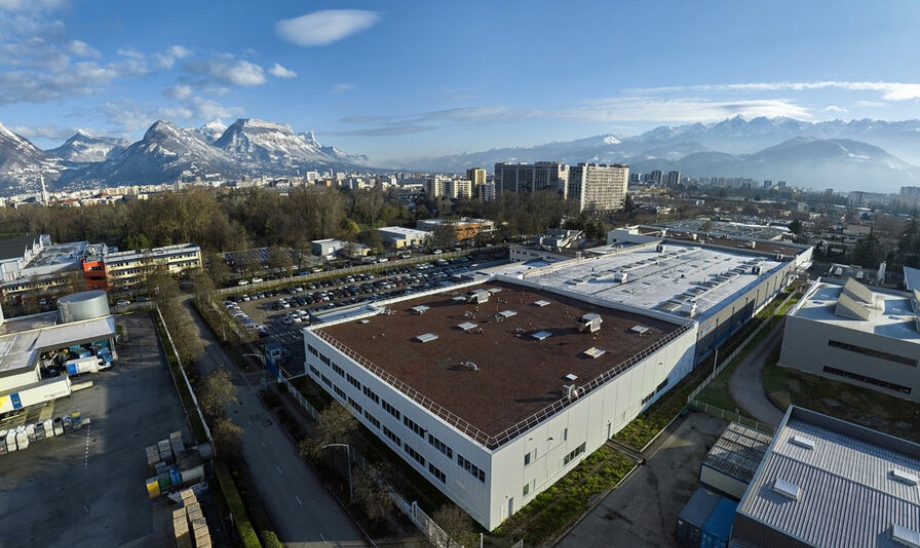
Sous le signe de l’excellence opérationnelle
« Nous sommes en pleine transformation digitale, » souligne Stéphane Bisiou, Responsable du bureau d’études de Minitubes. « Nos besoins de pilotage de notre outil industriel augmentent. Les transformations réalisées nous permettent de mieux développer de nouveaux produits, pour et avec nos clients. »
L’ambition est d’avoir à terme une usine totalement intégrée, avec des données disponibles au bon moment, au bon endroit et pour les bonnes personnes. Pour prendre la bonne décision, en temps réel, à partir d’éléments factuels, et dès qu’une dérive est constatée. Mais aussi pour identifier, en différé, les axes de travail et les chantiers d’amélioration à mener. En somme, avoir la bonne donnée, au bon moment pour répondre aux enjeux, à ceux des clients et plus largement à ceux du secteur médical. Car dans ce secteur, traçabilité et excellence opérationnelle sont de mise.
Schneider Electric propose donc une solution qui s’appuie sur des capteurs, intégrés notamment dans les moteurs, des automates ouverts qui collectent les données de tous les capteurs, un protocole sécurisé de transmission de ces données issues des différents automates jusqu’à une plateforme qui les analyse et les historise, et répond aux besoins de surveillance continue et de reporting.
« Par exemple, une « simple » surveillance et analyse conjointe du couple et de l’intensité du moteur permet de suivre l’effort d’étirage sur le banc et donc de s’assurer que tout fonctionne au mieux » explique Damien Bruno, chef de projet informatique industrielle chez Minitubes. L’interprétation de ces données permet d’anticiper des non-qualités : une consommation excessive d’électricité est le signe d’un moteur qui dysfonctionne, et donc produit mal. « Grâce à des mesures et à la mise en œuvre d’algorithmes de traitement sur le banc, nous analysons la qualité en temps réel. Cela évite de produire un stock de pièces non conformes, » explique Didier Champault, Responsable clientèle de Minitubes pour Schneider Electric France.
De plus, la traçabilité est assurée tout au long de la chaîne de production via des jeux de données sélectionnées aux étapes cruciales de production et archivées pour comparaison. Si besoin.
Près d’une centaine d’équipements existants sont d’ores et déjà connectés et remontent des données qui sont exploitées et permettent d’identifier les axes de travail et les chantiers d’amélioration à mener.
Transformation complète
Minitubes a pour ambition d’améliorer ses process, ses flux (internes et externes), et d’apporter de la modularité dans ses espaces. En digitalisant les outils de travail, l’ETI grenobloise peut déployer les méthodes de standardisation industrielle (4.0, refonte des méthodes de travail, 5S, lean) et de pilotage. Elle est en train de se doter d’un MES (Manufacturing Execution System), un logiciel collectant en temps réel toutes les données de production, données qui sont analysées en termes de traçabilité, de contrôle de la qualité, de suivi de production, d’ordonnancement et de maintenance préventive et curative. Minitubes est lauréat du Plan de Relance Industrie avec ses projets de développement, modernisation et digitalisation de son outil industriel.
En 2023, l’entreprise a finalisé une importante extension* de son site historique. Assurer tous les flux sans arrêt de production et sans rupture client est vital dans cette phase de forte croissance (doublement de l’activité et des effectifs).
Grâce à une stratégie claire, une intégration technologique réussie et un engagement envers l’amélioration continue, Minitubes attends entre 20 à 30 % de gains de temps de traversée et de productivité.
* Avec ce projet de réimplantation, Minitubes a reçu le « Trophée de l’Industriel qui développe son territoire » décerné par L’Usine Nouvelle.
Ajouter un commentaire