
Les industries du secteur du fer et de l’acier sont responsables de 9 % des émissions mondiales de CO2 et sont soumises à une forte pression de la part des gouvernements, des citoyens et de nombreux clients pour décarboner leurs activités. Par exemple, les principaux constructeurs automobiles exigent que les fournisseurs de composants en acier leur fournissent de l’acier vert (acier fabriqué sans utiliser de combustibles fossiles) pour construire leurs voitures et leurs camions. Cela permet en fin de compte de réduire leur empreinte carbone et, espérons-le, d’influencer les décisions d’achat des clients. Lisez notre blog pour découvrir comment les technologies de contrôle des processus contribuent à la mise en œuvre d’approches de production d’acier vert.
Les tendances technologiques telles que l’électrification et la production d’hydrogène permettent désormais à l’industrie sidérurgique de remplacer le charbon par des sources d’énergie propres pour produire de l’acier vert en quantités beaucoup plus importantes. Selon un récent rapport de l’ONG Global Energy Monitor, les fours électriques à arc représentent 31 % de la capacité actuelle de production d’acier.
Les régulateurs stipulent également que la production d’acier vert doit être soumise à un processus de certification impliquant une mesure et une déclaration précises des émissions de CO2. En conséquence, les fabricants seront taxés de manière agressive lorsqu’ils dépasseront certains seuils d’émission.
Les technologies hardware et software permettent de produire de l’acier vert
Les tendances du marché transforment radicalement la façon dont les entreprises sidérurgiques mènent leurs activités. Par exemple, des entreprises de premier plan telles qu’Algoma Steel et ArcelorMittal se convertissent à la fabrication d’acier à l’arc électrique afin de réduire les émissions de carbone de 60 à 70 %. Elles se positionnent pour une croissance à long terme sur le marché croissant de l’acier vert.
Prenons l’exemple du producteur d’acier européen Liberty Ostrava, qui est en train de transformer ses activités pour augmenter sa production d’acier vert. Il prévoit :
- D’investir des centaines de millions de dollars au cours des huit prochaines années pour atteindre la neutralité carbone d’ici à 2030.
- Le remplacement de ses quatre hauts-fourneaux traditionnels au charbon par deux fours à arc électriques hybrides.
- L’installation d’une infrastructure électrique modernisée permettant de produire de l’hydrogène et d’utiliser un plus grand volume de ferraille d’acier ainsi qu’une gamme plus étendue de substances de charge.
Ces stratégies réduiront la dépendance de l’entreprise à l’égard du charbon importé et réduiront considérablement les émissions de carbone.
Cependant, la modernisation des fours et de l’infrastructure électrique n’est qu’une partie de l’histoire de la décarbonation de l’acier. L’entreprise modernise également ses logiciels d’automatisation en vue de la mise en place des fours électriques à arc (EAF) et des capacités de traitement du fer à réduction directe (DRI). Le déploiement continu de la plateforme numérique AVEVA PI System permettra aux acteurs de l’aciérie de :
- Effectuer une analyse opérationnelle détaillée.
- Optimiser les systèmes existants et les nouveaux systèmes.
- Mettre en œuvre un programme en temps réel, basé sur l’état, pour la maintenance, le process, les émissions environnementales, la consommation d’énergie, etc.
Comment la nouvelle plateforme d’automatisation basée sur le cloud fonctionne pour l’acier durable
La maintenance conditionnelle permet d’identifier les problèmes émergents et d’appliquer des correctifs avant qu’une panne majeure ne se produise. Pour ce faire, elle recueille et analyse des données opérationnelles historiques et en temps réel, avec des conditions que les ingénieurs en fiabilité connaissent déjà.
Lorsque la plateforme identifie des anomalies, elle en informe les opérateurs qui peuvent prendre des mesures préventives pour éviter les temps d’arrêt. Outre l’amélioration de l’efficacité des processus de combustion et de conversion, le système de surveillance aide également les opérateurs à optimiser l’utilisation des matières premières et la consommation d’énergie.
Le AVEVA PI System peut avoir un impact positif sur l’efficacité opérationnelle et la rentabilité en permettant aux opérateurs de prendre des décisions meilleures et plus précises. Par exemple, en seulement un an, l’utilisateur du système Liberty Ostrava a réalisé une réduction de 10 % des pertes de production et a réussi une augmentation de 15 % de la qualité, économisant ainsi des centaines de milliers de dollars par mois. Au fur et à mesure de la mise en œuvre des nouvelles technologies EAF et DRI, ces économies peuvent augmenter de manière exponentielle.
L’entreprise a également déployé les solutions de jumeau numérique d’AVEVA ; un modèle virtuel, basé sur le cloud, que les ingénieurs peuvent utiliser pour tester la logique de contrôle à travers des graphiques d’opérateur dans un scénario de mise en service virtuel, minimisant les erreurs potentielles et rationalisant les processus de démarrage ou d’arrêt du système. Dans ce cas, le jumeau numérique offre une représentation visuelle des aspects électriques et d’automatisation de l’aciérie, avec la possibilité d’approfondir les aspects de l’opération liés au haut fourneau. Comme nous l’avons mentionné, des outils tels que le jumeau numérique ETAP peuvent simuler les caractéristiques du réseau électrique existant et tester et mesurer l’impact des changements apportés au système électrique d’une usine sans perturber le système en fonctionnement. Les ingénieurs peuvent utiliser ces deux outils pour optimiser les points de consigne tout en surveillant des paramètres tels que l’apport de gaz naturel ou les réactions chimiques. Il en résulte une réduction des émissions de carbone, une stabilité accrue du processus et des économies d’énergie.
En outre, AVEVA PI system peut consolider les données des capteurs et des équipements, ce qui permet une surveillance avancée des processus vitaux et une analyse avancée, en temps quasi réel, permettant des stratégies de maintenance améliorées telles que la maintenance prédictive et prescriptive.
Pour plus d’informations
Schneider Electric, AVEVA et ETAP sont au cœur des efforts de décarbonation de l’industrie sidérurgique. Nous fournissons des outils sophistiqués pour suivre les émissions de CO2 tout au long du cycle de vie de l’usine et soutenons les efforts de certification des fabricants d’acier. Pour en savoir plus sur l’accélération de la réduction des émissions de carbone et des coûts énergétiques dans l’industrie sidérurgique, regardez notre session maintenant.
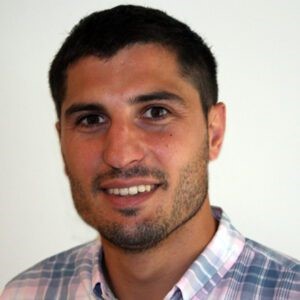
Geoffrey Scaringella est le directeur des ventes et du développement commercial de la société ETAP pour la France et l’Europe de l’Ouest. Il est né à Grenoble, en France, et est diplômé de l’école d’ingénieurs de Grenoble avec une spécialisation en sciences de l’énergie. Auparavant, il a occupé le poste d’ingénieur principal en systèmes d’alimentation électrique et a passé de nombreuses années à concevoir des systèmes d’alimentation pour les plus grandes centrales du monde.
Ajouter un commentaire