De nombreux producteurs ont limité leurs dépenses d’investissement, à moins que le projet ne promette un retour sur investissement très rapide, laissant certaines opportunités sur la table lorsqu’il s’agit de la durabilité commerciale à long terme. Un domaine qui ne doit pas être laissé inexploré est la nécessité stratégique de poursuivre sur la voie de la transformation numérique.
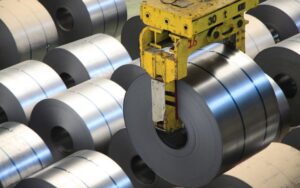
Les entreprises qui reconnaissent l’opportunité et agissent maintenant, même si le climat n’est pas idéal, se donneront un avantage concurrentiel qui durera longtemps dans le futur, et celles qui ne le font pas risquent de se laisser distancer. La question est de savoir comment évaluer la situation actuelle et investir stratégiquement dans les bons projets.
L’un des domaines où un retour sur investissement significatif peut être obtenu est le fonctionnement des ponts roulants, qui ont un impact considérable sur l’ensemble du processus de fabrication de l’acier, surtout si l’on considère l’âge et le manque de technologie de la plupart des systèmes utilisés aujourd’hui. Les ponts ont souvent plus de 30 ans et fonctionnent avec des technologies rudimentaires : logique de relais câblés, contacteurs et moteurs en ligne directe, et souvent avec une surveillance limitée.
Il en résulte un potentiel important d’amélioration de l’efficacité, de la productivité et de la sécurité, ainsi qu’une réduction des mauvaises manipulations de produits (qui se répercutent sur la qualité des produits et les dommages) et des temps d’arrêt. Ces aspects peuvent être considérablement améliorés par la numérisation, qui permet une augmentation de l’efficacité estimée entre 50 et 60 %, simplement en éliminant les goulets d’étranglement et les problèmes de manutention.
Un exemple auquel Schneider a participé ces dernières années est l’intégration d’un système de grue autonome pour cinq grues chez l’un des plus grands producteurs d’acier au monde. Dès le premier jour d’exploitation, l’entreprise a bénéficié des avantages immédiats d’un rééquilibrage des effectifs, puisque les grutiers pouvaient être affectés à d’autres parties de l’usine où les ressources étaient nécessaires. Puis, grâce à l’amélioration continue des opérations de grue, à l’augmentation de la productivité, de la sécurité et de la gestion des stocks, ils ont obtenu un retour sur investissement complet en moins d’un an.
Le système est basé sur des règles simples et des priorités de mouvement. Toutes les instructions sont exécutées en respectant les zones de sécurité configurées dans le système. La manutention est mémorisée avec une organisation optimale et les mouvements de grue les plus efficaces, sans cycle automatisé prédéfini et sans aucune interruption imprévue. Les grues sont complètement autonomes grâce à des algorithmes avancés à tous les niveaux du système (anti-basculement, trajectoires dynamiques 3D, détection d’objets, instrumentation intelligente…).
Connectées en temps réel à un progiciel de gestion intégré existant, les grues ne se déplacent pas seulement automatiquement, mais elles sont totalement intégrées au processus de production de bout en bout par la gestion du parc et l’orientation des produits entre plusieurs entrepôts. La gestion des flux de produits sidérurgiques au sein du site a pour but d’accélérer les transferts, d’optimiser les itinéraires, d’apporter plus de fluidité et d’éviter la saturation globale.
La numérisation peut-elle être la réponse à une production d’acier plus saine ? Pas sûr que ce soit la seule, mais la convergence IT/OT dans les opérations de grutage est un ingrédient clé pour une transformation numérique réussie dans la prochaine étape vers la productivité dans l’industrie de l’acier.
Schneider Electric dispose d’une équipe dédiée d’experts en levage qui peuvent vous aider dans votre parcours numérique pour atteindre les plus hauts niveaux d’efficacité dans vos opérations. Apprenez-en plus sur nous sur notre page dédiée aux solutions ou téléchargez la brochure dédiée aux solutions de Levage.
Ajouter un commentaire