A wise person once said, “The most valuable tool in maintenance isn’t a wrench—it’s foresight.” Reacting to issues after they occur doesn’t get the job done in today’s industrial landscape. Instead, you need to take a proactive approach to stay ahead of the game.
Shifting from reactive to predictive maintenance empowers businesses to stay ahead of equipment failures, and save time, money, and resources. In fact, it can reduce maintenance costs by up to 40% and increase equipment uptime by 9% on average. This transformation wouldn’t be possible without the role of advanced power monitoring systems. Connected devices and software collect and analyze voltage, current, and power quality data throughout your electrical network, enabling real-time insights that provide the data needed to make smarter decisions.
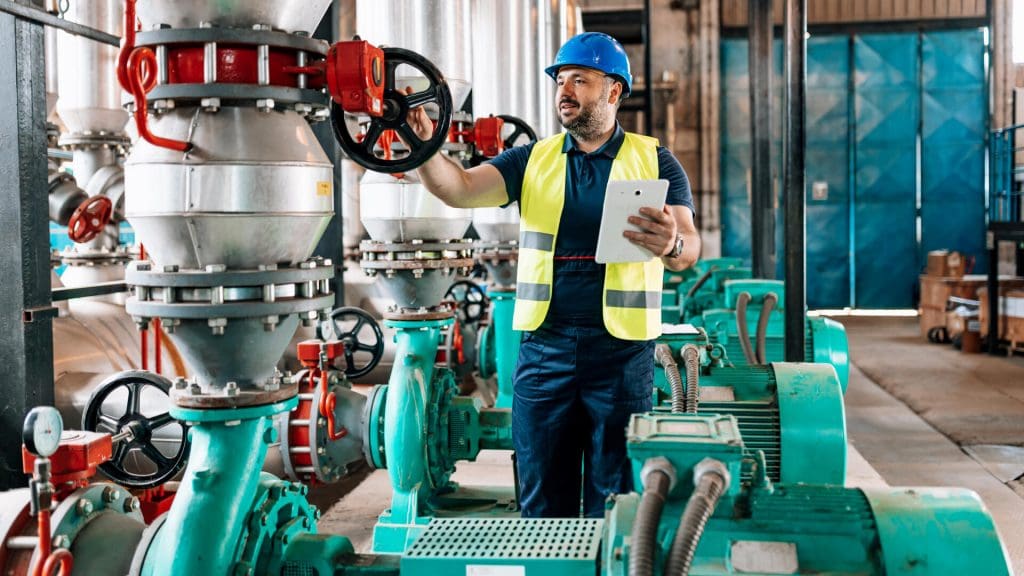
before they manifest as failures.
While this transformation may seem daunting, it’s actually not as difficult as you might think. Technological advances and data-driven tools have made adopting predictive maintenance more accessible than ever.
By leveraging advanced power monitoring systems, businesses can unlock the full potential of predictive maintenance. This enables more efficient operations, reduces downtime, and optimizes resource utilization. Using this approach, supported by AI and data analytics, enhances sustainability and cost-effectiveness – empowering organizations to stay ahead of aging infrastructure challenges while ensuring compliance and maximizing equipment lifespans.
Advanced power monitoring: The eyes and ears of predictive maintenance
The key enabler of predictive maintenance is the ability to monitor and analyze critical data points that reflect the health of equipment. Advanced power monitoring systems constantly scan for irregularities or patterns, allowing businesses to detect problems before they manifest as failures. Without these systems, companies are flying blind, reacting after an issue has occurred.
The main elements of advanced power monitoring systems are:
- Communication gateways connect various sensors, meters, and other equipment to a central system, and enable seamless data transmission over different protocols (e.g., Modbus, BACnet).
- Connected sensors use temperature, humidity, and moisture sensors to collect environmental data. This helps to detect conditions that affect equipment performance.
- Intelligent power meters measure electrical parameters like voltage, current, and power quality and communicate data in real-time for analysis.
- Energy management system (EnMS) software use specialized predictive maintenance modules that aggregate, analyze, and visualize data from all connected devices – providing actionable insights, alarms, and reports to optimize energy usage and maintenance.
Integrating suitable sensors and designing architectures prioritizing visibility is crucial to creating a maintenance strategy that minimizes disruptions and maximizes efficiency.
Efficiency, savings, and sustainability
Predictive maintenance goes beyond simply preventing equipment failures; it provides many benefits that enhance operational efficiency, generate cost savings, and support sustainability goals. Leveraging advanced monitoring and data analysis allows businesses to optimize their maintenance strategies and make more informed decisions. Here’s how predictive maintenance delivers value:
- Optimized maintenance schedules and cost savings: servicing equipment only when necessary reduces unplanned downtime and minimizes the need for excess spare parts.
- Enhanced operational efficiency: consolidating maintenance tasks allows businesses to strategically plan and bundle equipment downtime, improving productivity and maximizing resource utilization.
- Energy and waste reduction: equipment operating at peak efficiency helps lower energy consumption and minimize waste, contributing to a smaller carbon footprint.
- Improved workforce utilization: maintenance teams focus on high-priority tasks rather than constantly reacting to emergencies.
AI and analytics: The future of predictive maintenance
While advanced power monitoring systems already enable predictive maintenance, the future lies in integrating AI and analytics. These technologies push predictive capabilities to new heights and foresee potential issues more accurately. The challenge is that AI and analytics are advancing faster than traditional warranty clauses. Businesses may need to adapt their maintenance strategies to leverage these innovations fully.
AI-driven predictive maintenance tools analyze data in real-time, making it possible to anticipate when equipment will need attention far earlier than before. Over the next 5-10 years, we can expect AI to become a cornerstone of maintenance strategies, reshaping the industry’s approach to asset management and forcing companies to rethink their reliance on rigid maintenance schedules.
Practical considerations and service plans for advanced power monitoring
While predictive maintenance offers substantial benefits, you’ll still need expert support to best utilize it. A service plan can make all the difference in ensuring that your power monitoring systems are used to their full potential. Companies with service plans that not only improve equipment performance but can also extend warranties, making them a cost-effective solution in the long term.
These service plans ensure businesses have access to the expertise they need to interpret and act on the data collected by their power monitoring systems correctly. By partnering with experts, companies can avoid underutilizing their systems, maximize their investment, and keep operations running smoothly.
The future is predictive
Predictive maintenance, powered by advanced monitoring systems, is the future of efficient industrial operations. As AI and data analytics evolve, the potential for even more accurate predictions and streamlined maintenance strategies will only grow. Businesses that embrace predictive maintenance can reduce downtime, improve sustainability, and optimize their use of resources.
Explore our predictive maintenance solutions that integrate advanced power monitoring to stay competitive in today’s fast-paced industrial world. You can reduce costs, improve operational efficiency, and take a proactive approach to asset management that secures long-term success.
Add a comment