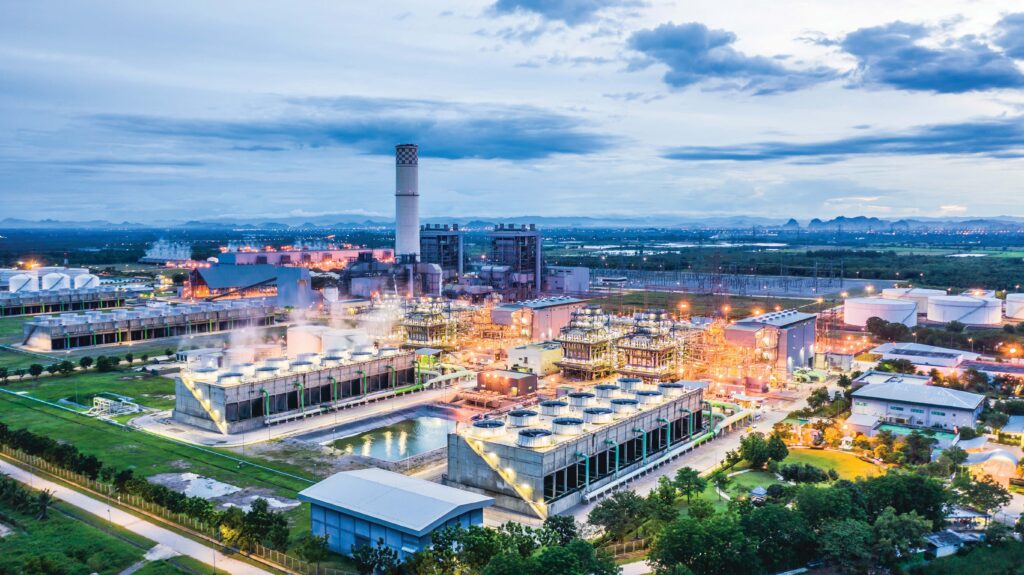
Controlling costs and remaining competitive continue to be important goals for any business, especially true in industrial automation. Deloitte recently identified some key trends for manufacturing operations, including the need to invest in smart technologies and smart factory transformation. The report notes that “companies with higher digital maturity have shown greater resilience.” The same is true for industrial automation, and high availability controllers can make that.
Risks to meeting this goal include increased customer demands and slow adoption of digital transformation. One of the biggest risks to this goal, however, is a lack of resilience against downtime. It’s estimated that factories typically lose 5 to 20% of productive capacity due to downtime. In the U.S., unplanned downtime losses are estimated at $50 billion annually, 42% of which is caused by equipment failure.
Ultimately, if a production line or process needs to be restarted or reconfigured, it must happen quickly and cost-effectively. The emergence of virtual, vendor-agnostic automation control with “bumpless transfer” can help industrial manufacturing and processing facilities future-proof operations while maximizing uptime.
Universal automation: future-proofing through portability
Ensuring industrial automation can meet the challenges of today and tomorrow requires digital innovation. While the innovations of the past were enabled within proprietary vendor systems, these closed systems now restrict progress. Digital transformation using software-driven solutions is only possible if your different vendor solutions communicate. More importantly, the solutions need to interoperate with each other seamlessly and without the need for any hardware and/or software gateway. An increased added value is being able to port your control application from one vendor platform to another. Control application portability is the true enabler to future-proofing your automation control system.
This interoperability and portability is now enabled with universal automation using a standardized automation layer. Schneider Electric is a founding member of the Universal Automation organization, an independent, not-for-profit association that welcomes users and vendors to share a source runtime execution engine designed to “unleash innovation by enabling application portability.”
With this collaboration, our EcoStruxure™ Automation Expert is the world’s first software-centric universal automation software platform, an open technology that can connect to Universal Automation complaint devices. This means that hardware and software are now decoupled to provide numerous benefits moving forward:
- Simplify plant modernization and speed failure response time. You can keep your control application programs and update/replace hardware, with the best choice available at the time, without being restricted to a specific brand. With the Schneider Electric SoftdPAC, you can run on any brand of industrial PC (IPC) as long as it meets the minimum requirements. Not being locked into one vendor’s hardware can help ease supply chain lead times by providing vendor flexibility.
- Simplify configuration. Use one engineering tool, configure the application once, and redeploy from vendor A to vendor B hardware without requiring a gateway or any customizations due to the vendor hardware chosen. This capability removes all the engineering effort that is required today when moving between vendors due to the lock-in approach of current DCS.
- Improve agility. With its development following the IEC 61499 standard, universal automation enables portability and interoperability. This allows proven-in-use software components to be used in a “plug-and-produce” approach to optimizing processes rapidly. This agility helps you respond more quickly to changing market demands while removing operational constraints to innovation and digital transformation.
Schneider Electric SoftdPAC meets high availability
For continuous processes, a business cannot afford a failure that can increase the cost of the process, lose a batch, or cause safety issues. All automation vendors have different levels of high-availability solutions using redundancy or fault tolerant methods. Bumpless transfer enables a seamless transition to a secondary controller in case of a failure in the primary controller hardware, ensuring that no physical controller hardware failure will put the continuity of a process at risk.
EcoStruxure Automation Expert now brings high availability to a more future-proof industrial automation platform with its release of the high availability version of the SoftdPAC. Leveraging the vendor-agnostic nature of universal automation, the high availability version of the SoftdPAC (a containerized version of the universal automation shared source runtime engine) can deliver bumpless transfer independent of the hardware that it’s running on. This is one of the first high-availability, software-based real-time controller in the marketplace.
It also supports controller and network redundancy between controllers for critical processes that can be implemented depending on the level of risks to production, safety, and the natural environment. Redundancy can be applied at the controller level and from the controller to the I/O modules. For example, in case of a network failure between the controllers, a backup network will ensure continuous communication and maintain the bumpless high-availability architecture.
This can help control costs and boost competitiveness by reducing downtime and supply chain challenges while simplifying plant modernization and making operations more agile.
To learn more, explore EcoStruxure Automation Expert or download the eGuide “Universal Automation – A call for change.”
Add a comment