It’s time for all medium and low voltage business stakeholders to address their carbon footprint
Today, electrical equipment manufacturers, contractors, and end users are taking their carbon footprints more seriously than ever. For medium and low voltage equipment, this means prioritizing a circular economy approach and sustainable equipment design that supports a low-carbon future. These sustainability improvements must also meet the UN’s sustainable development goals.
Innovative technology is essential for designing greener MV and LV equipment
Stronger decarbonization efforts can only be successful by adopting a circular economy approach that focuses on the entire lifecycle of medium voltage and low voltage equipment. The circular economy concentrates on reducing products’, services’, and systems’ environmental impact. It focuses on extending equipment’s useful life, reducing emissions and energy recovery, and promoting circular flows of materials.
Download our free MV technical guide to learn how you can design more sustainable MV installations.
Designing greener medium and low voltage equipment starts with a global value management approach that identifies which customers’ needs must be satisfied. This approach also identifies the needs of all stakeholders who are involved over the life cycle to determine the best way to minimize resource use (See standardized definition of value, p.78). This method is one of the best ways to design environmentally conscious products.
Manufacturers, panel builders, installers, and contractors can focus on maximizing medium and low voltage installations’ sustainability by using digital and connected ecosystems technology when designing and installing equipment or systems, such as medium and low voltage switchboards, transformers, and relays. Digital twins of equipment over its whole life cycle are particularly useful.
Data are the foundation of a green design
Many circular economy initiatives are launched and focused on the end goal, i.e., the highest level of analytics and methods (the engine) that deliver maximum benefits for stakeholders and electrical equipment users. However, initiatives should also prioritize data, which are the foundation of any digitalization plan. For example, data are used in the design stage to determine how durable the final installation will be based on information that is collected from connected equipment and devices. This ensures the final installation will meet end users’ values and needs.
Data management also allows stakeholders to anticipate decisions or actions to design more efficient, sustainable systems. This is possible because data is used to help stakeholders see and understand information that may otherwise be intangible (e.g., system overload, wear, and malfunctions). The data is defined by IEC technical committees in relation to the market needs. These data (from assets) are engine’s fuel control systems.
An example of digital data is the data needed to define products’ durability under normal conditions of use. During life cycle analysis, the reference service life is defined under a set of normal environmental and operational conditions. These “normal conditions” are defined by manufacturers. The data is collected using connected devices like sensors in medium voltage and low voltage equipment. Data are then analyzed to determine how to support lifetime extension, as well as future secondhand product and parts usage. This condition-based monitoring and material circularities are useful for assessing residual durability, meaning the ability of material, parts, and products to withstand future usages. The residual durability can vary from 0% to x%, depending of the previous life cycle and associated conditions.
For example, digital twins optimize MV and LV equipment’s design and performance
Digital twins are a good example of how technology enables environmentally conscious design. Digital twins are digital representations of a physical device or system in their circular environments. The digital twin model has an important role to play in equipment and systems’ decarbonization. That’s because giving data value at all steps of the product life (and project) enhances service life efficiency.
During the design stage, the digital twins are used to build and update a virtual model. Input simulates each step of the project on a single platform, such as equipment’s mechanical, electrical, thermal, and environmental properties. Digital twins provide a risk-free way to analyze, test, and experiment with different design scenarios, processes, equipment, and operations before making any changes to the physical asset’s design.
For example, when design is based on a functional analysis that reviews all functions needed over the whole life cycle, it will be obvious to stakeholders (e.g., specifiers, end users, contractors, or those using the digital properties, such as designers) how they can extract associated digital properties of this equipment both individually or when used into a system.
The following figure is a classification of digital properties that can be automated. The ability to automate is one main function and expectation of digital properties that feed electrical equipment’s digital twins.
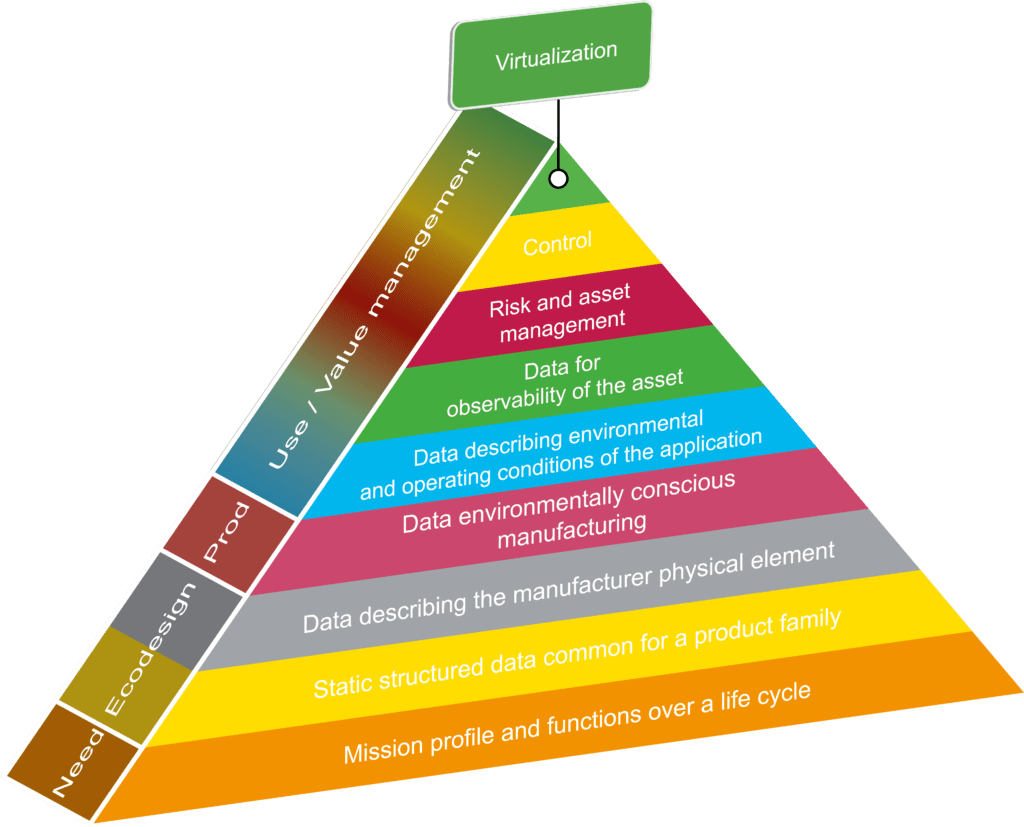
Classification related to the abilities of digital properties to be automated
For example, an electrical system digital twin analyzes the process impact and proposes the most adapted architecture. And, if relevant, the electrical system digital twin proposes an optimized power generation combination. For instance, it may identify how to maximize decarbonization by minimizing energy use.
Digital twins are also used for building information modeling (BIM) that is used for designing infrastructures. Digital twins are mainly used for BIM by applying mechanical representation while other aspects such as electrical, thermal, or control models are necessary. Many existing models, such as IEC 61850 or common information model (CIM), are used and recognized as interoperable to accompany smart grids in their transformation.
Learn how our innovative design eliminates SF6 use in MV switchgear
Our SF6-free MV switchgear is an example of how an environmentally conscious design based on technology creates a greener product. Rather than using the greenhouse gas SF6, MV switchgear has been designed to use only pure air and vacuum technology for breaking and insulation. For example, the electric distribution utility EEC Engie is using SF6-free MV switchgear to reduce the utility’s carbon footprint while maintaining the same level of safety, the same footprint, and minimizing changes to operations.
Learn how to create more sustainable MV equipment designs
Read our free MV technical guide for an in-depth look at how your MV installations will benefit from more technology-based, green designs. For instance, you’ll learn how sustainable design meets the UN’s Sustainable Development Goals and what technology you need to achieve them.Learn more about how MV equipment benefits from an environmentally conscious design.