This audio was created using Microsoft Azure Speech Services
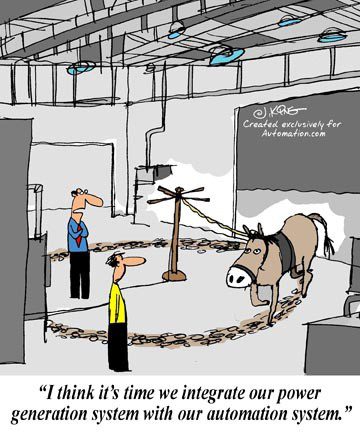
If you are a Plant Manager or work in Facility Operations at an industrial plant, you have a challenging job. Electrical systems, building systems, safety systems, process systems… the list goes on. And it’s your job to somehow be the glue that integrates it all. Corporate has almost certainly charged you with energy efficiency and sustainability mandates to meet. But you are flooding in data – big data, little data, data in silos. And if you hear the term Internet-of-Things (IoT) one more time, you are likely to throw a saucepan at someone.
Monitoring the overall energy use of a facility is certainly a no-brainer to improve your energy efficiency programs. But you can easily lose a lot of granular “process” energy data in the shuffle. Data that can have a significant impact on energy savings and the bottom line.
A laundry list of industrial energy management functions you might wish for:
- Isolate and categorize the cost of energy during various non-production periods.
- Relate energy costs more accurately to production costs
- Associate energy costs to units of production, progressing through the value chain
- Report metrics on departmental energy usage, separating production from facility energy usage
- Examine relationships of manufacturing processes to energy wastage
- Gather metrics to drive your ISO50001 programs, such as energy usage by processes idled, starved, or blocked, etc.
Historically, energy management systems look at energy data with an electrical system lens rather than from a process perspective. They may gather energy data at facility and sub-feeder levels, sometimes providing an incomplete plant view. Additionally, energy and process systems often function like spouses giving each other the silent treatment!
But a solution approach integrating the machine assembly or process system closely with the facility energy and power management system (EPMS), can provide valuable energy intelligence to help you make better decisions.
Process level energy management provides the following benefits.
- Correlate manufacturing processes to energy usage (e.g. process idling, process starved of parts etc.)
- Analyze energy and proactively alarm to isolate energy wasted during non-production periods
- Develop granular view of process energy usage and ways to achieve efficiencies
To prove that this kind of process-focused solution approach can be cost-effective, Schneider Electric implemented and tested it at two of its own Square D manufacturing plants. PowerLogic™ energy meters were installed at the process level of the plants. Process states and energy data related to ovens/paint lines and conveyors were integrated with the facility energy & power management software, StruxureWare™ Power Monitoring Expert.
By analyzing energy data trends across machine states, plant engineers isolated energy inefficiencies. They made appropriate operational adjustments to eliminate energy waste, providing significant savings. They also set up real-time alerting to proactively look for abnormal conditions creating energy waste, allowing even faster corrective action.
And the results were off the charts! A 31% energy savings was seen over a one-month period. A long list of positive results was seen, including reduced production overtime, increased reliability, and increased up-time, just to name a few. ROI payback for this plant project was less than 4 months. Extrapolating the results for facilities with larger scale motors, even more energy savings with a faster payback is quite likely.
Clearly, developing technologies in our Industrial Revolution 4.0 era will begin to incorporate machine learning systems that can identify anomalies using observed patterns. But this kind of process-level energy management is a concrete step you can take right now. This phased approach allows you retrofit your present process and controls with process level metering using nominal investment, rather than having to justify larger capex projects.
Go on, do a bit of judicious match-making: your energy and process systems can indeed be happily married!
Conversation
Bob Meyers
8 years ago
Clear and concise article of an excellent concept. Even better that it is field proven!