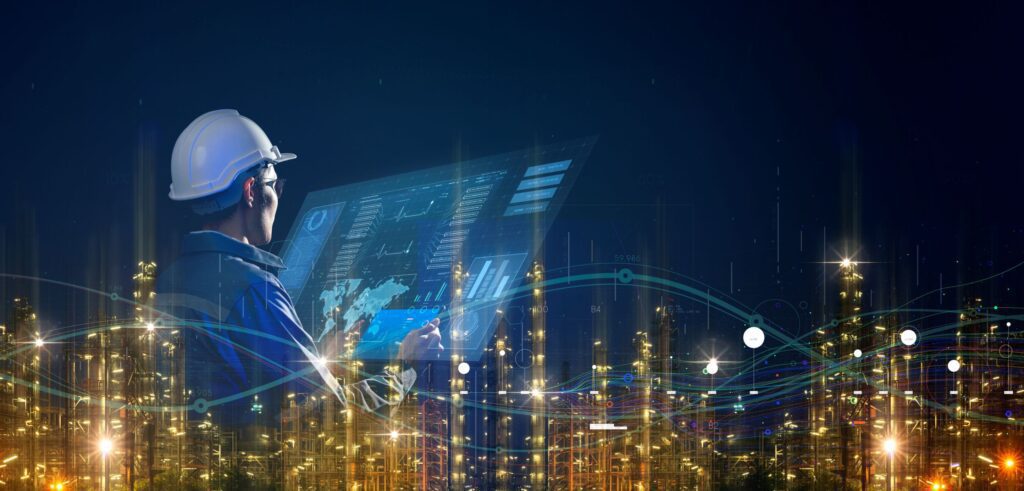
Today’s energy-intensive processes are looking to artificial intelligence (AI) technologies, including machine learning (ML), to help deliver smart automation capabilities needed to decrease machine downtime, expand asset utilization, and unlock immediate insights into real-time process optimization.
Organizations with a “digital-first” mindset understand the potential ML offers to vastly increase daily decision-making accuracy, speed, and flexibility. According to a recent study, 84% of C-suite executives believe AI is necessary to achieve their growth objectives, yet 74% concede that significant barriers to implementation exist.
Core constraints to building automated analytics into automation and control applications are a lack of access to technical skills, diversity in domain expertise, and deployment tools.
Numerous organizations, including Schneider Electric™, have found that a fundamental enabler of successful and ground-breaking ML deployment is to team up with expert outside partners. Dynamic collaborations can significantly enhance the skills and abilities of cross-functional and interdisciplinary teams. Such cooperation is the core philosophy behind our Partnerships of the Future program, an initiative designed to develop mutually beneficial professional relationships to speed innovation and generate superior business outcomes for customers and partners alike.
A collaborative approach to digital development strategy pays off
With valuable input from specialists at Alkhorayef Petroleum, Schneider Electric was able to develop edge analytics-enabled AI capabilities into the EcoStruxure™ Autonomous Production Advisor platform for oil and gas production facilities. It’s one example of the several successful digital co-innovation efforts Schneider is currently executing across multiple industrial segments. The goal of both partners was to build an AI-based solution incorporating ML and pattern recognition models that could detect anomalies in the Oil and Gas extraction process and positively impact several key challenges, including:
- Harnessing and replicating the insights and expertise of the most proficient well operators so their abilities could be automated and deployed across a broader range of production conditions.
- Actively managing equipment lifecycles to optimize well intervention schedules and generate maximum value from the physical asset base.
- Monitoring and reacting to downhole conditions in real-time to optimize petroleum production, reduce unplanned downtime, maximize oil volumes, and improve safety.
Because traditional automation architectures and strategies wouldn’t deliver the required capabilities, particularly for remote oil and gas wells, a new cooperative development approach was undertaken. Together, the team was able to leverage Schneider’s expertise in IIoT-enabled control systems and AI-based process optimization with Alkhorayef Petroleum’s knowledge and expertise of electrical submersible pumps to create novel techniques to capture and automate expert knowledge.
Cloud computing and edge analytics combined
EcoStruxure Autonomous Production Advisor merges the power and flexibility of cloud and edge computing with the value-generating capabilities of artificial intelligence and machine learning. In conjunction with remote terminal units (RTUs), the platform runs on industrial-grade edge controllers that combine supervised and unsupervised ML models running directly at the edge.
Replicating the actions of highly skilled human operators, the AI monitors the pump operation, assesses production variables, and analyzes the interactions and relationships between them, to identify anomalous operations. As a next step, the AI model classifies the detected anomalous events (such as sand intrusion, interfering gas, or mechanical problems) as specific issues. Continuous validation of the AI model’s event classifications by operators and experts helps to retrain the model, developing increasingly accurate diagnostic and predictive abilities.
The implementation of machine learning models in industrial applications forms an exciting new area because they can be trained to optimize operations and asset performance in a variety of important areas, such as:
- Identification of asset deterioration
- Early detection of abnormal behavior
- Prediction of equipment failure and smart alarming
- Asset performance management (digital twin)
An additional benefit of AI models is that such a solution can be trained for image recognition, enabling it to be an automation aid for several applications, including:
- Product quality
- Man down and intrusion detection and alarming
- Leakage detection and contactless flow measurement
- Machine vision and object and shape detection
Vendor-agnostic hardware enables the platform to be deployed to existing architectures without requiring significant modifications.
Co-innovation delivers tangible results
In offshore and onshore wells in the Middle East, Africa, and Latin America, the EcoStruxure Autonomous Production Advisor model training process has proven to be very effective at capturing the skills and expertise of the most senior operators and having the system automate and reproduce them. In one use case run by Schneider Electric, the customer reported a 13% increase in production and a 33% reduction in energy consumption.
Innovation isn’t just about technology; there’s no “one size fits all” strategy for partnering to invent new solutions that deliver major dividends. Success depends on nurturing conditions for a dynamic, mutually beneficial partnership. With a depth of co-innovation experience unrivaled in the smart control systems and process automation space, Schneider Electric is ready to work with true partners looking to overcome our greatest challenges.
Click to learn more about EcoStruxure™ Autonomous Production Advisor and Alkhorayef Petroleum.
Co-author
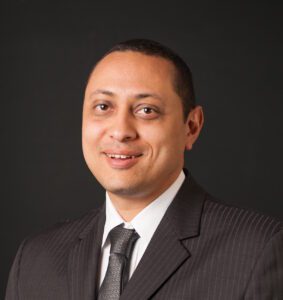
Khaled Elsheikh is Vice President of Artificial Lift at Alkhorayef Petroleum Company (APC), a position he has held since September 2018. Based in Dammam, Saudi Arabia, Elsheikh helps operators overcome the challenges of producing oil from the increasingly complex reservoirs the industry faces today. With his global perspective, Elsheikh is a recognized expert in Artificial Lift, where, prior to joining APC, he spent 16 years at Schlumberger.
At Schlumberger, he enjoyed a rich carrier that spanned many roles and different country assignments. Most recently, he was the Global Marketing and Technology VP for Schlumberger’s division of Artificial Lift. Elsheikh joined Schlumberger in 2002 as an Artificial Lift field engineer in the US after earning a master’s degree in Mechanical Engineering from the Imperial College of Science, Technology, and Medicine in the UK. Over the years, he has held a variety of positions around the world in R&D, strategy, quality, engineering, technology, and management. He has worked in eight countries and spanned several product lines, including wireline, artificial lift, and general oilfield services roles. He speaks Arabic and English fluently.