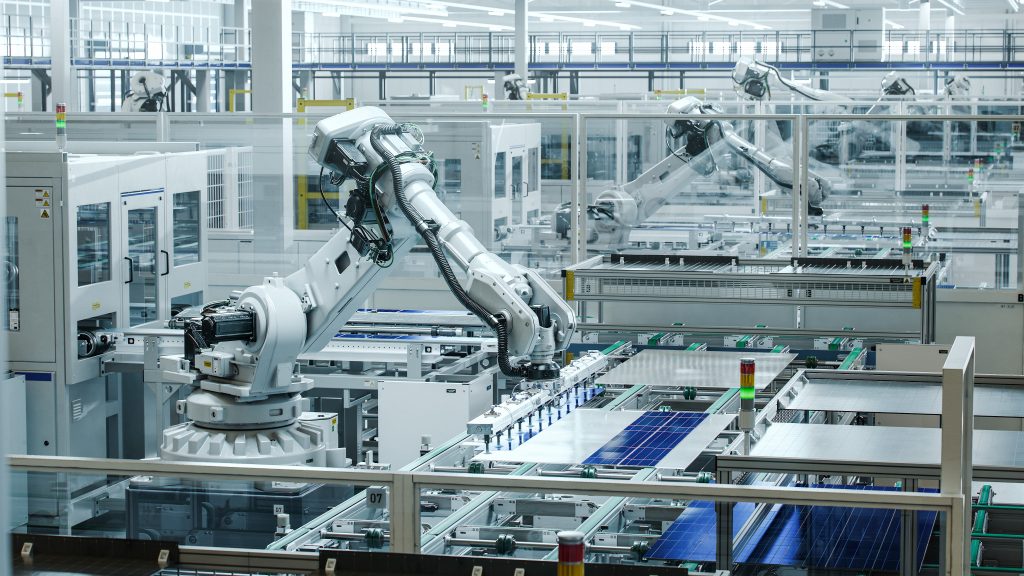
Having worked at the forefront of process automation for several decades, I have witnessed a profound shift in industry—brought on by digital technologies and artificial intelligence (AI). Traditionally, industrial companies prioritized cost, quality, and speed-to-market at the expense of sustainability. In fact, I would argue that sustainability was not even on anyone’s radar 20 years ago due to the limited understanding of global warming’s impact and the long-standing belief that efforts to reduce energy use and curb carbon emissions were too costly or difficult to integrate. Today, that imbalance is no longer necessary. Sustainable manufacturing is possible—thanks to significant leaps in technological capabilities.
Digital technologies and AI empower industrial leaders to optimize plant operations, improve resource efficiency across production lines and facilities, and implement smart controls that minimize energy consumption and emissions. Indeed, times have changed for the better. Yet we must act together quickly to make up for lost time—i.e., more than two centuries’ worth of carbon emissions since the dawn of the industrial age. As outlined in “Back to 2050,” limiting global warming to 1.5 degrees (compared to preindustrial levels) depends on getting carbon dioxide emissions to net zero by 2050. That journey starts with reducing emissions by 30-50 percent by 2030. That deadline is just around the corner.
Fortunately, we are currently witnessing ways for productivity and sustainability to be harmonized and help reduce industrial emissions. I was able to share my thoughts about this crucial topic at CERAWeek 2024. As I explained, since digital technologies provide the foundation for collecting, analyzing, and leveraging vast amounts of data, they can unlock unprecedented levels of transparency, reporting, and decision-making needed to navigate the complex landscape of sustainability.
Digital and AI can supercharge sustainable manufacturing in three key areas—at the machine, plant, and enterprise levels.
1. Reducing carbon emissions for sustainable manufacturing
At the machine or equipment level, predictive maintenance powered by AI is a game changer for reducing carbon emissions by optimizing asset performance. This is a win-win scenario, as advancements such as data analytics, machine learning, and IoT technologies also allow plant operators to maximize uptime by preventing equipment failures and prolonging equipment life. For example, we are working on a solution that leverages mounted camera(s), AI-computer vision, and edge computing to detect and quantify methane leaks. AI-powered predictive maintenance can determine the condition of a single production asset or entire system to avoid costs associated with shutdowns or maintenance. See again how productivity and sustainability can go hand in hand?
On a larger scale, for AI to make a tangible impact, it is critical not to treat it as a science experiment. Instead, consider the quantifiable business outcomes it can achieve, such as reduced metric tons of CO2 and avoided water waste. Abu Dhabi National Oil Company (ADNOC), one of the world’s leading energy producers, did just that by successfully creating a digital twin of their entire operation, using Schneider Electric and AVEVA software as their technology backbone. What was the impact? By integrating AI tools, ADNOC was able to abate up to 1 million tonnes of CO2 emissions between 2022 – 2023. And that’s just a start.
Similarly, working with Schneider, Duke Energy avoided approximately 2,000 metric tons of CO2 from being emitted per week through an AI-driven operational “catch.”
2. Optimizing energy demand for sustainable manufacturing
It is worth noting that more than half the decarbonization required to meet 2050 Net Zero Emissions targets will stem from demand-side changes (“Back to 2050”). At Schneider Electric, we like to acknowledge energy efficiency as the “first fuel” of the energy transition, powered by data-driven, digital insights, and AI. In fact, energy efficiency gains— optimizing final use demand—will contribute half of that. What’s the key enabler? Digitalization. Additionally, the Schneider Electric Sustainability Research Institute has found that 70% of CO2 emissions can be removed using existing technologies. If you ask me, I would say that we are in good shape to meet the biggest challenge of all time as the industry seizes the promises of digitalization and AI.
What does this optimization look like pragmatically? A Japanese refinery is using the power of AI to accelerate its safety, sustainability, and economic objectives. Using AI to model and predict outcomes, the team optimized processes to achieve 100% OEE and stabilize production flows, all while managing efficiencies and environment changes.
Digital and productivity go hand in hand, too. By leveraging digital twin technology, enhanced with AI & ML, one of the major players in the Energies and Chemicals industry is driving operational efficiency and minimizing wastage: 4,500 catches before start-up thanks to predictive modeling, saving cost, and improved decision-making throughout their operations.
3. Adopting renewable energy for sustainable manufacturing
Industrial companies are focused on applying digitalization to decarbonize existing plants and operations. This includes energy intensity improvements through optimization—producing the same with less energy—as this has clear efficiency-related OpEx benefits as well as modifying the energy mix. It also includes other operational improvements, sustainability (emission management and reporting), and data-driven decision-making.
For instance, ACCIONA Energía, the biggest 100% renewable utility without a fossil fuel legacy in the world, enabled optimization of energy recovery systems resulting in 4.6% reduction in energy consumption of the high-pressure pump and increased production capacity of the rack by 16 m3/h. The microgrid in the plant at Puente la Reina combines the production of renewable energy on-site, battery storage, and charging points for electric vehicles so that they can achieve maximum autonomy and optimize consumption in the grid.
Sustainable manufacturing’s bright future
AI, IoT, and digital twins form the digital foundation of sustainable manufacturing. By revolutionizing production processes, manufacturers can significantly improve energy efficiency, reduce waste, and enhance overall environmental performance across entire value chains. By focusing on material efficiency, minimizing waste, energy efficiency, integration of renewable energy, water efficiency, and wastewater management, industry stakeholders can accelerate efforts to achieve sustainable manufacturing.
Digital technologies play a transformative role in enabling end-to-end optimization across various disciplines, ensuring that the entire system operates at its highest efficiency while effectively managing resources and demand. Accordingly, sustainability is not just a compliance issue; instead, it is core to the modern operational excellence practice and, as a result, at the core of business performance. If done right, sustainability is an opportunity to reduce environmental impact but also to increase profitability, brand value, and recognition.
Now is the time for industry to make an impact—one that will last for generations.
Discover more about the impact next-generation digital technologies can have on the industrial energy landscape with Nathalie Marcotte, SVP and President Process Automation, in her panel interview at CERAWeek 2024.
Add a comment