This audio was created using Microsoft Azure Speech Services
The role of the human workforce in industrial digital transformation is one of the leading concerns companies have. Factors like cultural buy-in, retiring employees, and training are top of mind when it comes to undergoing the digital transformation journey.
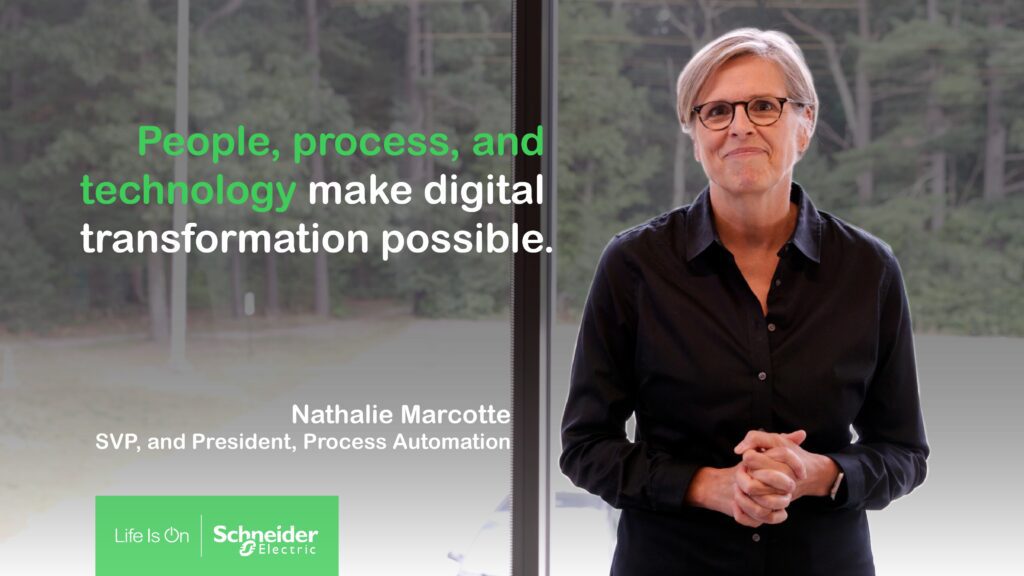
To help address that topic, I was recently interviewed on The Efficient Plant Podcast. Here is an excerpt of the conversation I had with Gary Parr, editorial director of Efficient Plant magazine, on how leaders can better prepare their companies for digital transformation.
(Editor’s note: This interview excerpt has been edited and paraphrased for clarity and length.)
Gary Parr: I was at a recent Schneider Electric event, and you were part of a panel discussion, and you brought up the human side of Industry 4.0. What about the people? It seems to me that doesn’t get enough attention, and it is an incredibly critical component, if people are going to be successful.
Nathalie Marcotte: When we discuss Industry 4.0, everybody gets super excited about this new and cool technology, but they don’t realize that technology alone is not going to make it.
We look at three core elements: people, process, and technology. Digital transformation will never be possible unless you address these three. People assume that workforces will get engaged and embrace Industry 4.0. But that’s not the case.
When you look at why digital transformation fails, a lot of the time it’s the lack of focus on people. We underestimate the change management effort that you must have either from the leadership level and on the shop floor at the operator level.
Whether it’s the technology or the people, it is not a one and done thing. It’s a process. It’s an ongoing journey, and people need to approach it in that way.
You need the sponsorship from senior management to make sure that digital transformation will be successful. There must be a focus on culture and continuous improvement from the management side.
Transformation fails if there’s a lack of continuous improvement, lack of transparency – it’s a top-down approach, you’re not engaging the people, you have limited site exposure versus an enterprise. [It fails if] you’re not empowering the people that will make this happen. It goes to my earlier point that transformation must be a back and forth with the people who are implementing these tools.
So, that says to culture. You need to change your company culture if you’re going to be successful. Step one, before you buy any sensors is, is to get your culture straightened out so that everybody feels like they’re part of the operation and feels like their input has meaning.
Yes, I think you need to engage the people. It needs to be a mix. You need younger people that understand digital. It’s in their DNA. They were raised around digital tools. But you also need the domain expertise of your most experienced talent.
If you don’t approach it with the right culture – the right approach – your senior staff will be disengaged and won’t be willing to share information because they feel their role will disappear and be replaced by a digital tool.
But that’s not the case. You want to capture that knowledge and then enable them to be more efficient. And once they learn this, then they engage. So, it’s clear at the beginning of the journey, you need to make sure that they realize the value they bring to this whole transformation, and not just the younger talent who have all these digital mindset and tools.
We’ve seen the result. When you do it right, engagement goes up. In some of our factories [that have undergone digital transformation], productivity has gone up.
Talk about training. Training in this environment – is it an ongoing thing, reinforcement? How does that fit into the picture?
It has to be tailored and at the right time for people. Once you’ve set your priorities for your digital transformation and the areas where you want to start… training needs to be meaningful. You have to identify the user, the people impacted, and build a plan for that group of people. It’s not a one size fits all training.
What has been your experience with repurposing people? Because a lot of this technology is designed to eliminate these redundant jobs, automate; and if handled right, take people’s talent, and use them somewhere where they can move the company forward, rather than sitting there putting a bolt in every three seconds. What has been your experience with moving people to other jobs and getting more out of their talent?
It has to be a bit of: What is that transformation going to do on the whole? Otherwise, if you only look at a given talent, maybe you’re not going to see the total picture of the impact of your workers at the beginning and at the end. And then, to your point, repurpose some of the talent depending on their background and know how, and find a new role or role that is (adjacent) to the role they were doing before, but that could have a better contribution.
Does the word “automation” still scare people in terms of taking away jobs? Or is that mindset changing and seeing the value?
You have to approach the people the right way. I’ve been in automation all my life, so automation never scared me. I think people, in general, see automation as something that will help do their job better.
But, again, you have to make sure you approach them if they have this fear, then that you overcome that fear. What I’ve seen is that people see automation as something that’s going to help me do my job better. There could be some cases where they’re worried and then you have to address it.
Be sure to listen to the full conversation between Nathalie Marcotte, SVP and president of process automation business at Schneider, and Gary Parr from Efficient Plant.
Add a comment