Opening and standardizing automation practices is not only beneficial to plant lifecycles but essential to our rapidly changing environment.
Roxann West, business development manager at Schneider Electric, was recently interviewed on the Energy Transitions Solutions Podcast to discuss how industries can accelerate their energy transition and sustainability. Here’s a snippet of what they discussed, diving into important subjects like universal automation, and how EcoStruxure™ Automation Expert helps accelerate the energy transition.
(Editor’s note: Parts of this transcript have been edited and paraphrased for blog.se.com.)
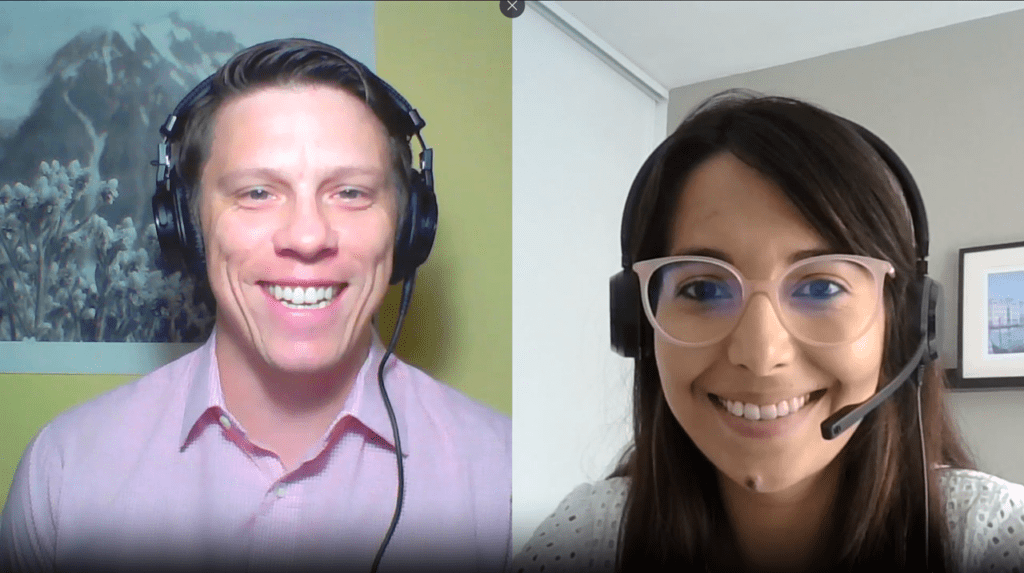
Growing trends in process automation
Joe Batir: What are some trends that you see in energy transition and challenges to further accelerate implementation?
Roxann West: Investments have significantly grown reaching over $1 trillion in 2022, and for the first time equivalent to that of fossil fuel investment, according to BloombergNEF.
Technology developments will accelerate this growth even further; as identified by energy and industrial executives in a recent study by Deloitte: more than 50% of them said that digital and operational technologies are priorities to improve operation and efficiency for a low-carbon future.
While there has been growth, there are still major challenges for acceleration. First is managing scalability and profitability – how to de-risk technology to scale and find profitable business model for them.
Second is the availability of infrastructure and skills – how to secure required investments, secure transportation, and to address the reduction of expertise with an aging workforce. How do we find new skills? New talent?
And lastly, how to upgrade and repurpose current assets efficiently. The trends for energy transition applications are that the processes are becoming modular. They need faster execution time from the pilot stage to large-scale production.
Some of the processes are also integrated into existing assets like carbon capture, blue hydrogen, green hydrogen, biofuels. So how can integrate these processes efficiently minimizing any disruptions to current operations.
And the critical role of process OEMs and licensors who are developing these new technologies… it’s very much a fragmented market with many niche players. So, the need to protect their IPs and provide fully automated packages becomes very important.
Now let’s dive into your focus area in process automation. How does automation system look like now, and what kind of constraints do you see for new energy applications?
Industrial automation has followed a different path compared with the IT world. It hasn’t changed much in the last 50 years since the first programmable logic controllers were invented. This is partly due to the over-reliance on proprietary systems, which pose barriers to innovation.
It’s not easy to run automation applications written for one system on another. This means making changes is slow and it’s costly to innovate or take on new approaches. There is a lack of standard objects to choose from, so it takes a lot of engineering to create a holistic plant architecture, leading to islands of control and inefficiencies.
Also, proprietary systems are difficult to maintain and expensive to upgrade. Unlike our phone or home computer, they’re not geared to take advantage of the latest advances in digital technology, so companies often don’t realize the full promise of digitalization.
With the new generation of talent, there is limited attractiveness for them to work on these old systems.
Now when we look at industries specifically, we see 30% of CO2 emissions are created by the industrial sector. We think the best way industries can mitigate this is through the combination of energy, automation, and software to reach their sustainability goals.
As of now, only 26% of industrial companies are reaping the rewards of digital transformation at scale – industries need an industrial software action plan to reach the next generation of industrial automation
Industries are now the No. 1 sector targeted by cyber criminals. So, effective management of people, processes, and technology is the key to resilience and efficiency.
The industrial sector is facing an expected shortfall of 8 million workers by 2030. So, how do we address that and have technologies that adapt new generation of skills and talent to make that attractive to them.
Overcoming process automation challenges
How do we begin to tackle these challenges and make automation for all?
Automation is not driven by hardware but software. So, how do we drive this while utilizing the same workforce. This new approach to automation will be compatible to Industry 4.0. We feel that software-driven digital transformation is fueled by increased computational power and connectivity.
We’re using the IEC 61499 standard, which is an event-driven, object-oriented, distributed approach. In turn, this is extending/enhancing the current IEC 61131 standard which is cyclical, allowing automation systems to take advantage of IT technologies. The IEC61499 standard addresses our customers imperatives for flexibility, interoperability, and efficiency.
In 2020, Schneider Electric became a founding member of a non-profit organization called UniversalAutomation.org, which is open and collaborative, based on the IEC 61499 standard. It introduces users to a world of “plug and produce” applications – think of it like an IT app store concept. It enables “à la carte” automation where cost and performance can be optimized by assembling different components independent of the vendor. In such a universal automation world, software is decoupled from the underlying hardware.
Essentially, it’s based on three building blocks:
- The IEC 61499 standard – a technology enabler
- A shared-source runtime execution engine
- And a community of users and vendors
The IEC61499 standard defines the portability and distribution of applications. The first part is the function block. The programming is object oriented linking the function blocks together. This way of programming can be both understood by people coming from the IT as for people coming from the OT field. The great advantage is the possibility to create black boxes to protect the intellectual property, and it enables the possibility to sell software components.
Then you create your application model on which you draw your application and the device model to create an architecture on which the software will run. After that you make the link with the physical world using the system model to connect to the inputs and outputs of your system. Finally, you can distribute your application on the available hardware.
We’ve used this concept of universal automation principles to create a next-generation automation system. It’s a software-centric automation application called EcoStruxure™ Automation Expert. People can build applications using software components that are “portable” and easy to install on any automation hardware.
These applications can be deployed across different types of system hardware, architectures, or components with minimal programming effort. You can also incorporate edge computing for more intensive applications. And then the processing load can be shared across all available hardware resources.
EcoStruxure Automation Expert allows you to realize the benefits of the fourth industrial revolution, helping you work towards:
- 100% Engineering Efficiency – Low- or no-value-added tasks become automated, eliminating duplication of efforts when moving from one engineering tool to another.
- 100% Operational Effectiveness – Engineers are provided with the tools they need to maximize asset uptime and to optimize workforce efficiency.
- 100% Future Proof – Applications that engineers work on are now future-proof. A wrap and reuse approach can be used to support current systems while allowing full application portability for future migrations.
Examples of software-centric applications
Do you have examples of how EcoStruxure Automation Expert has helped accelerate growth in energy transition applications?
We have a couple use cases implemented. One was for Wilo’s green hydrogen pilot plant in Germany. The solution enabled them to homogenize their heterogenous system and provide flexibility to expand and replicate their modular plant more efficiently as they plan to scale.
Similarly, a plastic recycling pilot plant also adopted this software-centric, vendor-agnostic approach to close the loop for waste disposal by recycling over a ton of plastic per day. This solution enabled them to expand process capacity without additional programming, significantly reducing engineering time and time-to-market. The company has built two pilot plants with plans to replicate and scale.
Be sure to listen to the full conversation between Roxann West, business development manager at Schneider Electric, and Joe Batir from Energy Transitions Solutions Podcast.
Add a comment