A pandemia alterou as tendências de procura dos consumidores e as capacidades dos fabricantes para fornecerem bens ao mercado – algo que aconteceu em todos os setores. Para se adaptarem, muitas empresas estão a repensar o potencial papel da digitalização e das máquinas inteligentes para as ajudarem a redesenhar as operações de forma a serem mais ágeis. A flexibilidade de produção é fundamental, uma vez que melhora a capacidade de uma empresa para configurar linhas de produção mais rápidas e mudanças de produção para acomodar mudanças de mercado frequentes e rápidas. O desafio é introduzir estas novas capacidades sem gerar custos excessivos ou investir em recursos humanos adicionais.
Para apoiar esta mudança, tanto os OEMs (fabricantes de equipamento original) – que desenham, comissionam e dão suporte às máquinas que servem de base às operações industriais digitalizadas – como os utilizadores finais – que operam as máquinas – vão ter de reavaliar a forma como aplicam as tecnologias de digitalização a um “novo normal” cada vez menos previsível.
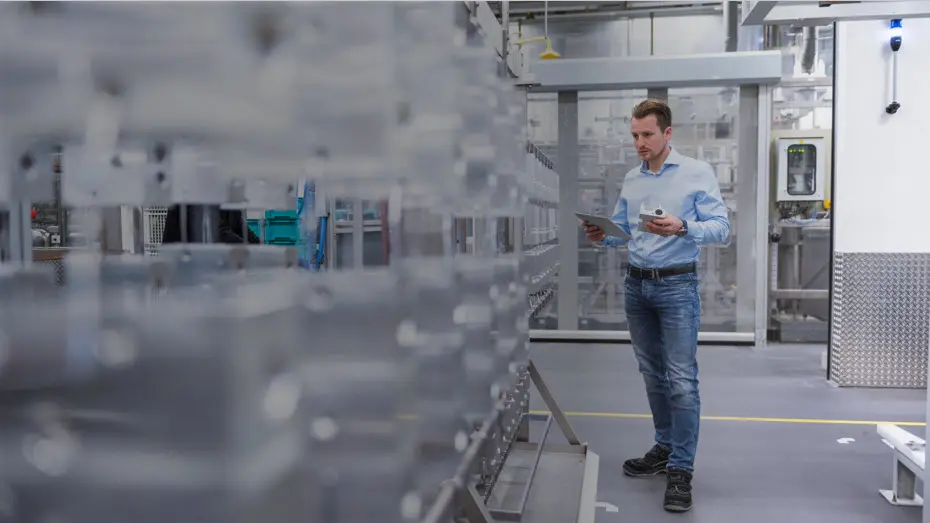
Como a digitalização beneficia todo o ciclo de vida das máquinas inteligentes
Estabelecer uma infraestrutura sólida de máquinas mais eficientes, flexíveis e ágeis implica a integração de máquinas mais digitais, que desbloqueiem um novo potencial de negócios e melhorem a eficiência.
Eis as três fases do ciclo de vida das máquinas onde a digitalização das operações resulta frequentemente em ganhos de eficiência e num rápido retorno do investimento:
- Design da máquina – Na fase de design e engenharia, as capacidades de engenharia e simulação automatizadas estão a reduzir o tempo de comercialização em até 30%.
- Comissionamento e operação da máquina – Durante estas fases do ciclo de vida da máquina, a integração dos OEMs, o comissionamento e a eficiência do suporte operacional podem ser melhoradas em até 40%.
- Manutenção e assistência técnica das máquinas – Nesta fase de assistência, a eficiência e a agilidade são proporcionadas por máquinas conectadas que permitem uma manutenção preditiva através do acesso e monitorização remotos, num ambiente de cibersegurança. Estas ferramentas de suporte digitalizadas podem reduzir o tempo das ações corretivas em até 50%.
Uma abordagem digital à construção e operação de máquinas implica melhor conectividade, maior mobilidade, acesso a computação Cloud económica e análises ricas. Os benefícios da digitalização incluem a utilização otimizada de recursos e a capacidade de tomar decisões inteligentes mais rapidamente, melhorando também a capacidade de serviço para reduzir drasticamente o tempo de inatividade.
Como o utilizador final beneficia: um exemplo real de uma máquina inteligente
Um fabricante de chapas flexográficas (chapas utilizadas para fins de impressão) identifica o seu diferenciador de mercado como uma combinação de produtos de alta qualidade e tempo de entrega rápido. Para apoiar estas vantagens competitivas, o fabricante exige que o OEM da sua máquina providencie não apenas equipamento de qualidade, mas também um pacote de serviços excecional. O fabricante quer que o OEM esteja “sempre atento” a ele, para que seja possível ter sucesso na maximização do tempo de atividade da fábrica e da qualidade do produto. O OEM cumpre este requisito de serviço ao conectar-se remotamente às máquinas do fabricante e monitorizar o seu desempenho. A conectividade remota permite que o OEM permaneça sempre disponível para o fabricante, mesmo durante um período muito difícil de disrupção, como foi o da pandemia.
As máquinas funcionam de forma altamente eficiente, com muito pouco tempo de inatividade, uma vez que o OEM tem acesso remoto aos seus dados de desempenho e pode acompanhar os parâmetros da máquina remotamente, de forma contínua e quase em tempo real. O OEM também implementa ferramentas de software que permitem a simulação da máquina, que pode ser melhorada através de dados relevantes desta ao longo do seu ciclo de vida. Como resultado, o OEM é capaz de prever quando a máquina pode vir a falhar e, assim, resolver com antecedência situações potencialmente problemáticas, minimizando qualquer possível disrupção das operações.
Os dados da máquina são recolhidos e sincronizados com câmaras que fazem parte da configuração da máquina (juntamente com as ferramentas de gestão de ativos Schneider Electric Edge Box e EcoStruxure Machine Advisor). As gravações da câmara são armazenadas na Edge Box no local (um servidor local concebido para funcionar em ambientes industriais), criando dados históricos em tempo real. Se uma máquina parar, o OEM pode reiniciá-la imediatamente de forma remota e analisar os dados mais tarde para determinar a causa principal da interrupção. Esta abordagem revolucionária é completamente diferente das situações tradicionais, em que a máquina permanece inativa, retida num estado de erro e à espera de uma intervenção no local para retificar o problema. A câmara remota proporciona visibilidade física da máquina ao longo das várias fases do seu ciclo de vida e é capaz de sincronizar os seus parâmetros operacionais com qualquer evento preciso, de forma a otimizar a eficiência do desempenho da máquina.
Para mais informações
Para serem bem-sucedidos neste novo ambiente, mais dinâmico e imprevisível, tanto os OEMs como os utilizadores finais têm de desenvolver novos conjuntos de competências. Estas competências devem centrar-se em conseguir uma maior agilidade operacional e tirar partido da inteligência sobre a procura em tempo real para melhorar a visibilidade do processo. O objetivo último é aplicar os benefícios da digitalização – tempos de ciclo mais rápidos, maior eficiência, menor custo e melhor suporte às decisões – a todo o ciclo de vida das suas máquinas.
Visite a página do EcoStruxure Machine Advisor para saber como esta plataforma digital pode trabalhar no sentido de minimizar os tempos de mudança de produção para os fabricantes e simplificar a gestão do ciclo de vida das máquinas para os OEMs.
Adicione um comentário