CONDICIONAMENTO DE AR PARA REDUZIR A TEMPERATURA DE COMPONENTES COMO VARIADORES DE FREQUÊNCIA, PLC’S DE ALTA DENSIDADE E PAINÉIS MICRO PROCESSADOS É ESSENCIAL EM AMBIENTES COM APLICAÇÕES DE MISSÃO CRÍTICA.
A medida que componentes eletrônicos estão reduzindo de tamanho, seus circuitos eletrônicos ficaram mais compactos, e a velocidade de comunicação aumentou, porém, a densidade de carga dentro dos invólucros cresceu e, juntamente com ela, a quantidade de calor rejeitado. Habitáculos muito justos e painéis elétricos e de automação com restrição para passagem do ar aumentam rapidamente a temperatura interna causando falhas de controle.
Industrias tradicionais como de bebidas e alimentos, químicas, farmacêuticas, tratamento de água e esgoto, petroquímica e mineração estão sendo direcionadas cada vez mais para o mundo de “IoT” (Intermete das Coisas), se tornando dependentes de “PLC’s” (Controlador Lógico Programável), variadores de frequência e microprocessadores altamente sofisticados. Como resultado, a dissipação de calor adequada se torna essencial para proteger esses componentes sensíveis, tornando-os missão crítica ao processo produtivo.
Ensaios térmicos em quadros elétricos e de automação envolvendo condicionamento por convecção natural, ou até mesmo por ventilação forçada, método mais comum e com maior troca de ar (em média 10x mais que a primeira opção), não são mais adequados para o resfriamento de componentes eletrônicos dentro de ambientes fabris onde a temperatura interna pode passar dos 35°C com facilidade. Pesquisas realizadas por fabricantes de sistemas de controle apontam que a cada 10°C de aumento na temperatura, a taxa de falha de componentes eletrônicos aumenta em 40%, e paralisações de produção on-line dobram. A maioria dos fabricantes de componentes eletrônicos estabelece os máximos limites de operação em 40°C e 90% de umidade relativa.
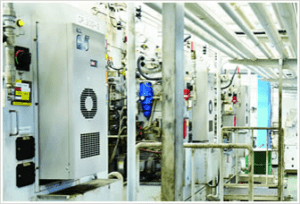
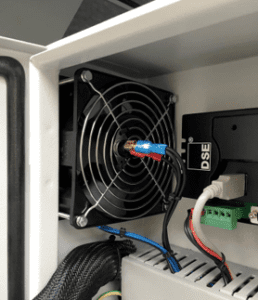
Adiante estão expostos alguns pontos de vantagem e desvantagem dos métodos de condicionamento de ar em quadros elétricos e de automação projetados para ambientes fabris:
- Ventilação forçada:
- Relativamente barata e fácil de instalar
- Depende bastante da temperatura interna da fábrica.
- O ar proveniente do ambiente fabril forçado para dentro do quadro pode conter gotículas de óleo aerossol e outros contaminantes não visíveis que cobrirão a superfície de circuitos eletrônicos caros, sensíveis e essenciais ao processo fabril.
- Expansão direta:
- Controle maior de temperatura durante o ano.
- Se for equipamento do tipo “self-contained” (Condensador e evaporador dentro da mesma máquina), a temperatura interna da fábrica é um limitante.
- Espaço físico de instalação e infraestrutura disponível.
- Alto custo de manutenção e instalação comparado ao sistema de ventilação.
- Necessita de tratamento especial em seus componentes se instalado em ambiente de atmosfera agressiva
- Expansão indireta:
- Mesmas características do sistema de expansão direta, porém, podendo ter custo de implantação mais elevado.
- Depende da disponibilidade de água gelada no empreendimento.
- Requer mais atenção na montagem dos componentes do sistema hidráulico para evitar vazamento de água gelada no quadro.
Saiba mais no site apc.com!
Conversa
joão marcelino
1 ano ago
boa tarde,
gostaria de receber o e-mail de compras para que possa ser enviado uma apresentação.
att